AL-KO booste sa production grâce à la robotique de Yaskawa
YASKAWA / AL-KO
parLa société AL-KO, située à Louhans au nord de la Bourgogne est mondialement reconnue pour son savoir-faire dans le domaine de la fabrication d’essieux destinés aux véhicules de loisirs et aux remorques. Elle s’est récemment équipée d’une nouvelle cabine de robotisation, comportant un robot de soudage ainsi qu’un deuxième robot pour les mouvements de manipulation.
L’activité principale d’AL-KO réside dans la fabrication de composants pour remorques et caravanes (essieux à éléments caoutchouc, commandes de freinage, timons, etc.) et dans des adaptations sur véhicules utilitaires (essieux à barres de torsion rondes et dans la réalisation de châssis pour camping-cars et camions magasins), sans oublier la distribution d’équipements et d’accessoires pour les véhicules routiers. Le bureau d’études, constitué de quatre personnes, travaille principalement sur des standards développés par le groupe, lesquels sont ensuite adaptés pour répondre au mieux aux besoins des clients français. Par exemple, dans le domaine du camping-car, le châssis AL-KO et l’essieu sont fabriqués sur mesure avec des empattements et porte-à-faux variables en fonction du cahier des charges du constructeur offrant ainsi de multiples possibilités d’aménagement intérieur et d’espace de rangement.
Devant la croissance de la demande du marché, en particulier celui des véhicules de loisirs qui ne cesse d’augmenter (17 414 immatriculations de camping-cars neufs en France en 2015 soit une hausse de 12,7%), une nouvelle cabine de soudage robotisé fut planifiée en remplacement d’un ancien robot qui commençait à donner des signes de faiblesse. Un nouvel investissement s’imposait donc pour stabiliser et fiabiliser le process.
L’évolution du cahier des charges
Au début du projet, le cahier des charges que proposait AL-KO, était bien éloigné de la solution globale. À cette époque, l’équipe technique d’AL-KO pensait réinvestir dans un même type de robot (de type 6 axes, soudage en MAG) et réaliser tout simplement un « copier/ coller » de l’ancienne station. C’est alors que toute une équipe chargée des études de nouveau projet chez Yaskawa, fabricant de robots et spécialiste en automatisation, s’est penchée sur l’ensemble des besoins et a proposé de tenir compte des tâches pénibles de manipulation consistant à relier une bride de 5 kg et un tube de 10 kg, ayant une forme finale assez difficile à manoeuvrer tant par rapport au poids total que, surtout, par sa forme peu ergonomique. Un deuxième robot fut alors proposé au client, réduisant considérablement la partie manipulation, et ce avec un gain de temps non négligeable.
Un résultat probant
Aujourd’hui, cette cellule autonome fonctionne à temps complet avec des programmes capables de fabriquer 6 types de produits différents (4 nouveaux produits devraient être affectés à cette cellule d’ici fin 2016). À la fin du cycle, le robot de manipulation dépose le produit fini sur un chariot, appelé « sapin », recevant les pièces terminées. Ce chariot sera ensuite transféré pour un traitement ultérieur (usinage, graissage, peinture et vernis) avant l’assemblage définitif sur châssis. L’opérateur n’intervient que pour déposer les différents composants pour le cycle suivant à l’endroit de stockage prédéfini pour le robot, et ainsi de suite. Un retour sur investissement rapide Anthony Orblin, du Service Méthodes chez AL-KO n’a pas longtemps hésité pour valider ce projet. « Nous avions déjà 4 cabines de robots au sein de notre production, nous confirme ce dernier. Le choix fut rapidement validé par notre direction. Nous pouvons affirmer aujourd’hui que le retour sur investissement sera atteint en trois ans, ce qui est peu pour une installation qui tournera pendant dix ou quinze années. L’autonomie gagnée sur ce type d’installation à double robot nous offre un avantage non négligeable : pendant que la cellule travaille de manière autonome, l’opérateur est affecté à d’autres tâches. De manière générale, nous pouvons affirmer que la robotisation ouvre de nouveaux champs d’innovation et de productivité dans l’usine. Maintenant que cette cellule est implantée, cela nous donne plein d’idées pour la suite ».
Bruno Rodrigues, technico-commercial robotique Yaskawa, va encore plus loin dans son analyse. « La France n’a pas assez investi pendant ces dernières décennies et les robots sont encore aujourd’hui trop peu présents. Contrairement à des pays comme l’Allemagne, la robotisation n’en est qu’à ses débuts en France, elle n’est pas encore entrée dans nos gènes. Les industriels se posent des questions sur la complexité d’une telle mise en place, sur la fiabilité et le prix d’acquisition. Dans les années à venir, une fracture très nette risque de s’opérer entre les sociétés industrielles qui ont réussi à prendre le train en marche, tant que leur marge de manoeuvre le leur permettait, et les sociétés trop frileuses par rapport aux investissements nécessaires. En effet, la mondialisation a poussé un grand nombre de sociétés à délocaliser leur production, tandis qu’une simple robotisation aurait pu faire l’affaire. Et nombreuses sont les sociétés qui réintègrent aujourd’hui leur production en France ».
« Une nouvelle tendance s’ouvre désormais, poursuit-il. Des sociétés productrices de robots où les intégrateurs dépassent de plus en plus souvent la préconisation d’une simple station de soudage. C’est l’ensemble d’un processus qui est pris en compte, depuis le chargement des composants jusqu’au déchargement de la pièce ou du sous-ensemble finis. Désormais, la nouvelle norme qui semble s’installer durablement consiste à affecter deux robots dans la même cellule : le robot principal est assisté par un deuxième robot qui lui fournit les composants. L’intérêt économique est indéniable ».
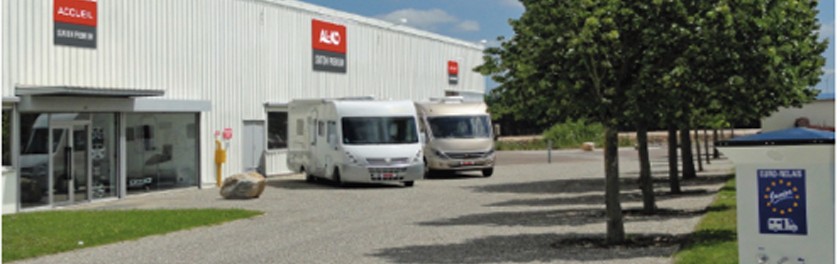
La Station Premium AL-KO est heureuse d’accueillir le grand public à Louhans (71) sur une surface de 200 m². Sa vocation est d’apporter aux caravaniers et campingcaristes un service à la hauteur de leurs attentes ainsi que le conseil et le savoir-faire d’un professionnel de la suspension pour le montage d’accessoires en post-équipement et l’entretien.
• Yaskawa expose sur Industrie Paris, Hall 5E54
N° 75 avril 2016