Partenariat pour la fabrication additive métallique
RENISHAW /I3D CONCEPT
parQuand il est possible de remplacer un sous-ensemble composé d’une douzaine de pièces par un corps monobloc réalisé en fabrication additive métallique (FAM ou ALM) assurant les mêmes fonctions, il y a immanquablement un niveau de création de valeur qui ne laissera pas indifférents les protagonistes.
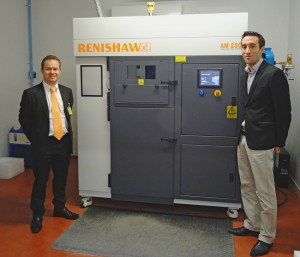
Entourant la machine de fusion laser AM 250 Renishaw, M. Tisserand Responsable
produits et le dirigeant de i3D ; M. Péjoine situé à droite sur la photo
La fabrication additive pour ambition
Depuis de nombreuses années, ce challenge semble tout naturel à Jean-Baptiste Péjoine. En 2015, il a fait l’acquisition d’une machine de fusion laser Renishaw AM 250 et réunit autour de sa société, i3D Concept, un collectif de partenaires lui permettant une expertise que lui envieraient nombre de grands groupes et de clusters : « Notre société s’est dotée d’une machine pour développer un savoir- faire dans cette technologie en devenir et constituer d’ici un à deux ans un pôle de fabrication additive de grande capacité. Cependant, la vocation de notre groupement est, prioritairement, d’accompagner les TPE et PME dans leurs projets de fabrication additive métallique et ceci dès la phase d’avant projet. »
Le choix du fournisseur n’est pas anodin. Renishaw apporte un accompagnement de proximité, sous la conduite de Christophe Tisserand responsable produit pour la France. Avec l’appui de « Solutions Centres », Renishaw facilite la montée en compétence de ses clients dans des domaines qui dépassent largement le cadre de la formation au pilotage de la machine. Ils incluent la conception des pièces, le développement matière, la caractérisation des pièces, etc. Ce spécialiste de la fabrication additive par fusion laser sur lit de poudre dispose de machines évolutives et configurables telles que AM 250 et AM 400 orientées sur la R&D et RenAM 500M, dédiée à la production. L’inventeur du palpeur à contact est aussi un utilisateur de référence qui produit au sein de sa division médicale et dentaire jusqu’à 4 000 pièces en chrome-cobalt par mois.
Tout un pôle associé au projet de FAM
L’arrivée de cette première imprimante métal était préparée depuis deux ans et attendue par l’ensemble des partenaires associés : M-Tecks EAC (bureau d’études), Groupe Danielson (volet industriel et production), Nicolaïe MTP (expertise matériau), CIMMES (laboratoire ingénierie mécanique). L’équipe d’i3D s’est immédiatement consacrée à déployer le programme de travail sans pour autant brûler les étapes : prise en main, expérimentations à partir de prototypes fonctionnels ou de pièces existantes, mais intéressantes pour leur morphologie.
La fabrication additive métallique est un process complexe où l’on crée un matériau par fusion. La densité, la granulométrie, l’état de surface et les propriétés mécaniques dépendent des stratégies de programmation qui régissent l’épaisseur des couches de poudre, la taille du faisceau laser et son parcours. La conception et les posages de la pièce sont également des facteurs très importants à optimiser. En tenant compte des limites de fabrication, toute matière déposée a besoin de support pour ne pas s’affaisser, il est possible d’améliorer la fonctionnalité d’une pièce tout en réalisant des gains de masse et de temps de production très importants.
Il faut considérer l’impression métal comme une étape d’un processus plutôt qu’une finalité. Sur ce point, Jean-Baptiste Péjoine et Christophe Tisserand partagent une vision commune : ce n’est pas la machine qui crée le plus de valeur mais bien ce qu’elle a permis d’obtenir, d’où l’importance de partir d’un projet conçu dans la logique FAM. Sans être exhaustif, il est permis de citer quelques applications remarquables à leur actif : le nouveau dispositif de refroidissement d’un moule d’injection, dont les réseaux d’alimentation ont été conçus à partir des possibilités offertes par la FAM, a permis de gagner 40% de productivité chez l’injecteur. La réduction du nombre de composants d’un ensemble, les gains de masse et leur impact sur des systèmes en mouvement comme dans l’aéronautique, la création de formes complexes intérieures dans les secteurs hyperfréquences et électromagnétiques… sont des gisements de valeur qui deviennent accessibles avec la FAM.

Traitement thermique, usinages et opérations de parachèvement font souvent partie du
process global en fabrication additive par fusion laser
Une confiance réciproque entre Renishaw et son client
A la fois accompagnateur et premier témoin du chemin parcouru en 2015 par i3D Concept, le responsable produit Renishaw se félicite de la démarche et des résultats obtenus par le tandem formé par Jean-Baptiste Péjoine et Amaury Chavanon, responsable production et pilote de la cellule d’impression métal AM 250. « Leur équipe a une capacité à intégrer tous les points d’analyse pour progresser sur les plans de la métallurgie, du contrôle de la matière, du contrôle des formes intérieures grâce au contrôle non destructif, de la caractérisation d’une pièce et des stratégies d’impression qui en découlent ». Accompagnant cette montée en technologie, Renishaw est plus que jamais au service de son client i3D Concept afin de l’aider à accroître son savoir- faire en fournissant du service, des conseils et de la matière. Pour l’industrialisation de pièces très techniques, Jean-Baptiste Péjoine a déjà fait appel à son fournisseur pour le développement de deux nouvelles références matières utilisables en FAM. C’est une compétence interne pour Renishaw qui nécessite deux à trois mois pour la recherche et la mise au point des paramètres avant que le client puisse industrialiser son process.
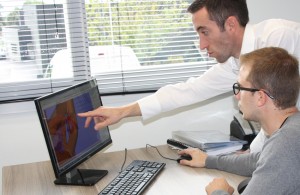
La recherche des meilleures stratégies de parcours du laser permet d’améliorer la productivité et les caractéristiques qualitatives de la pièce à produire.
Du pôle de fabrication au pôle de compétences partagées
Après cette première étape d’exploitation, le bilan machine est très satisfaisant pour l’utilisateur. La machine Renishaw AM 250 prévue pour une production de petites séries ou de pièces unitaires, comme le prototypage, dispose de possibilités de paramétrage très étendues permettant de répondre aux attentes de R&D souhaitées par le dirigeant de i3D et ses partenaires associés. Amaury Chavanon apprécie sa flexibilité lui permettant d’effectuer les changements de matière appropriés aux applications qui se succèdent. Équipée des logiciels QuantAM ou Magics + BP, l’AM 250 bénéficie d’outils évolutifs pour l’importation de fichiers CAO et le pilotage de stratégies d’impression. De même que les modèles de production AM 400 et RenAM 500M, le modèle AM 250 réussit la prouesse d’une faible consommation énergétique, un critère qui compte pour Jean-Baptiste Péjoine.
i3D Concept avance entourée d’un réseau d’expertise à 360° et de partenaires impliqués dans le processus FAM. Cinq machines de production viendront progressivement constituer le pôle de fabrication additive de la structure. Renishaw et i3D Concept, chacun dans leur rôle, mettent leurs compétences au service des PME qui souhaitent se lancer de façon sécurisée sur le créneau de la fabrication additive par fusion laser.
N° 72 février 2016