Assurer la qualité des pièces produites pour l’aérospatial en fabrication additive
EOS / MTU AERO ENGINES
parPour tester les composants fabriqués de manière additive, MTU Aero Engines s’appuie sur la surveillance active couche par couche du processus de fabrication à l‘aide d‘Eostate ExposureOT.
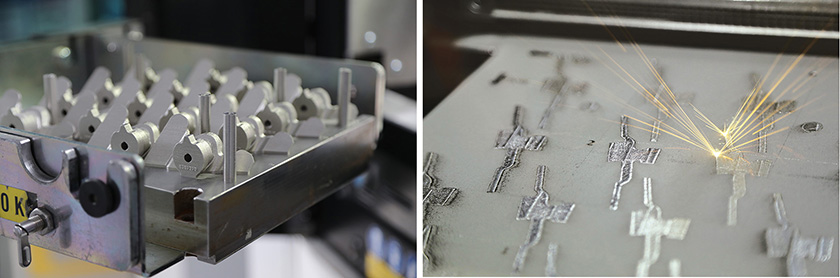
Production en série par fabrication additive de moyeux endoscopiques pour turboréacteurs à réducteur d‘Airbus A320neo.
(Source : MTU Aero Engines)
Les composants produits pour l’industrie aérospatiale doivent remplir des critères d’assurance qualité stricts. Dans les environnements de production en série, les normes de qualité des composants sont particulièrement élevées, et la stabilité et la reproductibilité du processus extrêmement importantes. L’assurance qualité est donc cruciale tout au long de la chaîne de production.
Il y a encore quelques années, il n’existait pas de procédures de test bien établies dans le domaine de la fabrication additive. Des processus non destructifs en aval, comme les essais de ressuage, les rayons X et la tomographie par ordinateur (CT), étaient utilisés pour les composants métalliques. Bien que ces méthodes de test classiques soient un bon moyen de certifier les composants dans certains cas, elles sont extrêmement onéreuses et souvent insuffisantes. Le coût de l’assurance qualité peut être bien supérieur à celui de la production.
« Eostate ExposureOT nous signale toute pièce susceptible de présenter des défauts. Nous avons pu supprimer tous les examens par rayon X et CT dans la production en série de moyeux endoscopiques, ce qui, économiquement parlant, s’avère extrêmement avantageux. »
Karl-Heinz Dusel, responsable de la technologie de fabrication additive chez MTU Aero Engines
Le défi à relever
Les nouveaux processus de fabrication additive s’accompagnent de défis majeurs dans le secteur de la construction de moteurs en raison des règles de certification de sécurité extrêmement strictes. Tout composant destiné à voler doit faire l’objet d’une surveillance constante, de la matière première au produit fini, pour s’assurer qu’il ne présente absolument aucun défaut. De nouvelles méthodes et idées économiques s’imposent pour mettre en œuvre une assurance qualité qui couvre la technologie d’impression/de test 3D industrielle, le contrôle de processus et la documentation. MTU Aero Engines a commencé à développer la tomographie optique en 2013 afin de trouver une procédure de test spécifique pour surveiller et documenter intégralement les processus de fabrication additive.
Les phases initiales de recherche et d’implémentation ayant été un succès, l’entreprise a continué à développer cette technologie dans la solution Eostate ExposureOT en partenariat avec EOS GmbH. Le système surveille l’environnement de fabrication tout entier avec une caméra industrielle sCMOS et mesure en haute résolution les émissions thermiques du processus de fusion. Le logiciel configurable fournit des informations détaillées sur la qualité de chaque couche des composants. La tomographie optique permet de contrôler la reproductibilité, d’accroître la comparabilité entre les composants, les projets de fabrication et les systèmes d’impression, et de mettre en œuvre une assurance qualité à moindre coût dans les applications de fabrication en série. MTU Aero Engines souhaite maintenant utiliser Eostate ExposureOT comme procédure de test des composants fabriqués de manière additive et ainsi réduire les coûts d’assurance qualité.
La solution mise en œuvre
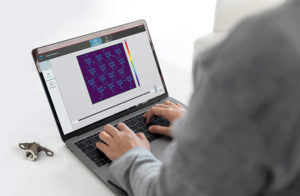
MTU Aero Engines s’appuie sur la surveillance en direct couche par couche du processus de fabrication à l’aide d’EOSTATE ExposureOT pour tester les composants produits en FA (source : MTU Aero Engines)
MTU Aero Engines utilise Eostate ExposureOT depuis plusieurs années dans la production en série par fabrication additive, notamment pour le développement de processus et l’assurance qualité des moyeux endoscopiques des turboréacteurs à réducteur nouvelle génération de l’Airbus A320neo. L’entreprise a ainsi acquis une solide expérience de ce processus d’assurance qualité et a pu effectuer des comparaisons avec d’autres technologies non destructives. Dans un premier temps, les composants série ont été inspectés à l’aide d’examens radiographiques et CT classiques parallèlement à la tomographie optique, et les résultats ont systématiquement été comparés.
Il s’agissait de répondre à ces questions : Eostate ExposureOT peut-il détecter tout type de défaut possible, y compris les cavités, les pores, les inclusions solides ou les fusions incomplètes avec autant de fiabilité que les méthodes de test classiques ? Eostate ExposureOT peut-il accroître la probabilité de détection (POD) ? L’entreprise a aussi établi systématiquement des comparaisons avec des méthodes de test destructives, comme les inspections au microscope des sections transversales et des échantillons. Les essais ayant démontré la fiabilité de cette technologie, MTU a été convaincu par son efficacité et a décidé de déployer cette nouvelle assurance qualité. L’entreprise utilise maintenant la procédure de surveillance active couche par couche du processus de fabrication par Eostate ExposureOT pour tester les composants fabriqués de manière additive.
Aucune pièce défectueuse n’a été omise
Lorsqu’il a été établi qu’Eostate ExposureOT détectait de façon fiable tous les défauts potentiels d’une production en série, MTU Aero Engines a franchi un cap. Les comparaisons entre Eostate ExposureOT et les méthodes classiques d’examen radiographique, CT et destructif ont montré qu’Eostate ExposureOT augmentait la probabilité de détection par rapport aux autres méthodes non destructives, notamment pour les fusions incomplètes. Ce qui signifie que toute erreur détectée par des examens RT ou CT est aussi clairement identifiée par Eostate ExposureOT. « Eostate ExposureOT nous signale toute pièce susceptible de présenter des défauts. Il n’en a omis aucune jusqu’à présent, explique Karl-Heinz Dusel, responsable de la technologie de fabrication additive. Nous avons ainsi pu supprimer tous les examens par rayon X et CT dans la production en série de moyeux endoscopiques, ce qui, économiquement parlant, s’avère extrêmement avantageux ».
À l’avenir, le fabricant de moteurs allemand prévoit de mettre à niveau Eostate ExposureOT pour passer d’une simple technique de surveillance du processus à une méthode de test officielle. Le contrôle statistique du processus simplifie aussi considérablement l’évaluation des résultats. Il suffit de quelques tâches de fabrication sans défaut pour définir une courbe fiable d’écarts tolérables et remplacer un processus d’échantillonnage parallèle. Des tests supplémentaires ne sont réalisés que lorsque des écarts sont constatés.
EQUIP’PROD • N°113 octobre 2019