Mobilité en transition : de nouveaux défis pour de nouvelles solutions
MAPAL / HELLER
parLa mobilité électrique prend de plus en plus d’importance dans l’industrie automobile, et le nombre de véhicules électriques produits augmente régulièrement. Mapal offre déjà une large gamme de solutions d’usinage innovantes pour la fabrication de pièces et de composants.
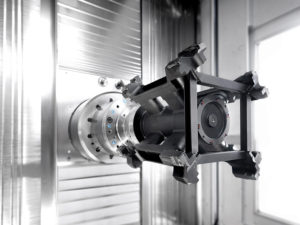
Pour la fabrication de l’alésage principal du carter au micron près, l’usinage est réalisé avec un outil de finition de Mapal
Les moteurs électriques et autres éléments des véhicules électriques sont des composants auxquels les constructeurs automobiles et leurs fournisseurs accordent une grande attention depuis un certain temps déjà. La conception de nouvelles pièces et leur fabrication en série représentent souvent un défi, et les tolérances serrées exigent un savoir-faire spécialisé. En 2017, Mapal a travaillé avec le constructeur de machines-outils Heller pour relever ce défi et préparer les process de fabrication d’un nouveau carter pour la production en série.
Le constructeur allemand de machines-outils Heller avait en effet reçu une demande d’offre pour la conception et l’usinage complet d’un nouveau carter de stator, incluant les machines, les outils, le process, les dispositifs de prise de pièce, ainsi que le traitement de toutes les données correspondantes. Le projet était ambitieux, le client final ayant fixé un délai très serré pour les travaux. De plus, les exigences imposées au composant étaient très élevées et les tolérances très étroites. « Ce carter spécial était une pièce entièrement nouvelle pour tous les partenaires, y compris pour notre client », se souviennent Dietmar Stehle et Tobias Schur, respectivement responsables des outillages et de la conception d’outils chez Heller dans ce domaine.
Dès l’étape de planification pour la préparation de l’offre, Heller a fait appel à Mapal en tant que fournisseur d’outils. « Dietmar Stehle et Tobias Schur sont venus nous voir très tôt pour la mise en œuvre de ce projet », explique M. Meier, membre responsable de la force de vente de Mapal. Dans ce type de projets, en particulier dans le cas des nouvelles pièces, il est en effet capital de s’assurer que tous les intervenants sont en concordance dès le début.
Ensemble, Heller et Mapal ont donc conçu le process complet pour l’usinage de cette nouvelle pièce. L’un des avantages de ce travail en commun de plusieurs dizaines d’années, a été que les deux entreprises ont pu s’atteler directement à la tâche en formant une équipe bien coordonnée. Ils ont ainsi étudié la conception de l’outil proposé par Mapal, et examiné le process. « En travaillant étroitement ensemble, nous avons trouvé la conception d’outil idéale pour l’usinage », poursuit M. Meier. Et ce sous une énorme contrainte de temps, se souvient Dietmar Stehle : « pour ce projet, nous avons dû livrer les premiers prototypes très rapidement ». Ceci alors même qu’ils étaient en train de mettre la dernière main au processus de moulage de la pièce.
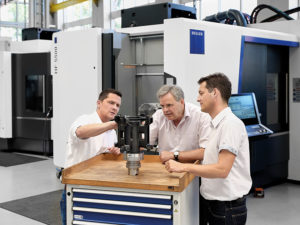
Les caractéristiques impressionnantes de l’outil comprennent son faible poids et ses arêtes PCD finement réglables
L’alésage du stator comme le plus grand défi
L’usinage de l’alésage principal du carter s’est avéré être le plus grand défi de l’ensemble du processus de fabrication. Un domaine bien connu du groupe Mapal, car l’usinage de finition fiable et économique d’alésages profonds de grands diamètres est l’un des domaines où il excelle.
Le fabricant d’outils fortement lié à l’industrie automobile a acquis cette expertise grâce à des décennies d’expérience dans des domaines tels que l’usinage de carters de boîtes de vitesses. « Nous avons mis à profit notre savoir-faire et l’avons appliqué aux exigences de la pièce du client », indique M. Meier. Pour ce projet commun, Mapal a opté pour des outils légers et extrêmement robustes en construction mécano-soudée, parfaitement adaptés à l’usinage des parois minces. Malgré la grande longueur hors tout et le grand diamètre de plus de 250 mm, l’outil obtient des résultats de haute précision.
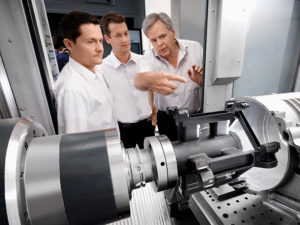
Les spécialistes Heller Tobias Schur et Dietmar Stehle (de droite à gauche) ont travaillé avec M. Meier de Mapal pour déterminer l’outil parfait
Légèreté grâce à la conception tubulaire
Pour les outils de conception mécano-soudées, on utilise une construction tubulaire pour le corps de l’outil. Ces outils ne pèsent que la moitié du poids d’une barre d’alésage conventionnelle. Les supports pour les arêtes de coupe et les patins de guidage sont soudés et sont reliés entre eux par une ossature spécialement étudiée pour son poids réduit. Cette conception permet de réduire les vibrations et assure également un soutien lors des coupes interrompues. La résistance à la flexion est excellente grâce à cette conception tubulaire et à l’ossature de stabilisation.
« Nous avons divisé l’usinage de l’alésage principal en trois opérations : ébauche, demi-finition et usinage de finition », ajoute M. Meier. Dans la dernière étape, l’alésage principal est usiné avec une précision au micron grâce à l’outil d’alésage de précision de conception mécano-soudée. Les plaquettes de coupe équipées de PCD disposent d’un réglage fin pour obtenir une précision maximale. Pour un soutien optimal dans l’alésage, l’outil est également doté de patins de guidage de haute précision.
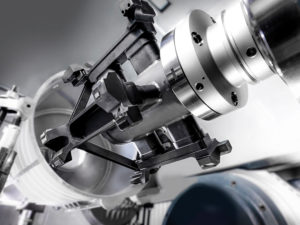
La combinaison du centre d’usinage Heller et des outils de Mapal fonctionne avec succès en production en série
Mise en œuvre réussie dans la production en série
À l’image de cet alésage, les experts du fabricant de machines et du fabricant d’outils ont également trouvé des solutions appropriées pour toutes les autres opérations d’usinage. « Ensemble, nous avons démontré que non seulement l’usinage complet de la pièce dans les tolérances spécifiées fonctionne bien, mais aussi que la solution mise en œuvre permet un process fiable dans les temps de cycle requis », résume Dietmar Stehle avec satisfaction.
Les deux partenaires Heller et Mapal ont acquis un savoir-faire précieux au cours de ce projet en commun. De cette coopération sont nées des solutions entièrement nouvelles, notamment des outils à alignement automatique permettant d’atteindre les tolérances de positionnement cruciales, en raison de l’usinage par retournement nécessaire de la pièce. En bref, les deux entreprises ont réussi à concevoir le processus de fabrication parfait dès la première phase d’études. Aujourd’hui, le client fabrique cette pièce avec un volume de production à cinq chiffres.
EQUIP’PROD • N° 111 Juin 2019