Miser sur la fabrication additive pour plus de productivité
MAPAL
par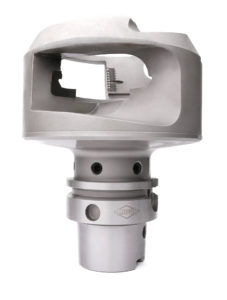
› La structure en nid d’abeille à l’intérieur de l’outil peut être réalisée grâce à une fabrication additive.
Outre la liberté de conception, la possibilité d’optimiser le poids est l’un des avantages essentiels de l’impression en 3D. Grâce aux structures spécialement développées à l’intérieur de l’outil, qui ne peuvent pas être fabriquées de manière conventionnelle, le poids peut être réduit de manière significative, à l’image du nouvel outil à cloche de Mapal ; celui-ci, en plus d’un poids réduit, affiche une longue durée de vie et de meilleures données de coupe.
La façon dont Mapal utilise les avantages de l’impression 3D dans la pratique s’illustre par le nouveau système de cloche avec des inserts en PCD brasés. Les outils en cloche sont utilisés pour l’usinage extérieur des raccords de tuyaux, entre autres applications. Ces raccords, utilisés par exemple sur les turbocompresseurs, doivent répondre à des exigences de contour complexes. La fabrication doit être d’une précision correspondante. Les processus existants font également l’objet d’une amélioration continue afin que la fabrication soit rentable et fiable dans la production en série.
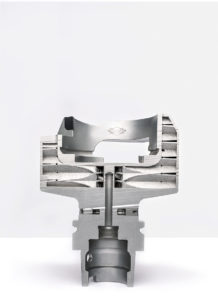
› Mapal présente un nouvel outil à cloche avec un faible poids, une longue durée de vie et les meilleures données de coupe.
Mapal a souhaité optimiser l’outil à cloche existant, fabriqué de manière conventionnelle. Grâce au procédé de fusion sélective au laser, l’intérieur de l’outil a été modifié ; au lieu d’un matériau solide, une structure en nid d’abeille a été spécialement conçue. Ainsi, l’outil s’est allégé de 30 % et sa durée de vie a été augmentée d’environ 40 % grâce à l’effet d’amortissement. Il est donc possible d’usiner plus rapidement ; la qualité d’usinage reste au même niveau élevé. Au total, le temps d’usinage a, quant à lui, été réduit de 50 %. En outre, la conception du canal de refroidissement a également été optimisée.
Le nouvel outil à cloche repose sur une conception hybride. Grâce à la fusion sélective au laser, la nouvelle géométrie de l’outil est imprimée sur un corps d’outil précis avec une connexion HSK-63. La pièce fabriquée en additif est ensuite usinée de manière conventionnelle. Les inserts en PCD sont ensuite brasés en place et découpés à la forme voulue à l’aide d’un laser.
EQUIP’PROD • N° 115 février 2020