Figeac Aéro rationalise l’usinage avec les fraises Mitsubishi Materials pour mieux accompagner sa croissance
MMC METAL FRANCE / FIGEAC AÉRO
parMaîtriser n’est pas simple. Et Figeac Aéro le sait plus que quiconque. Pour maintenir le niveau de qualité optimal de ses pièces et répondre aux montées en cadence, l’entreprise lotoise a choisi d’équiper ses machines de fraises Mitsubishi Materials AXD4000 pour l’usinage des alliages d’aluminium. Cet outil a entièrement répondu aux exigences de l’entreprise qui a bénéficié en outre d’un accompagnement technique du carburier japonais.
Si la ville de Figeac est peu connue des Français, elle s’illustre dans le monde de l’industrie comme une des rares communes d’à peine 10 000 habitants abritant des grands noms de l’aéronautique, à commencer par Figeac Aéro. Ce fleuron français de l’aéronautique a suivi les géants du secteur, tels qu’Airbus, dans leurs montées en cadence. Et les chiffres sur les perspectives de croissance listés par Nicolas Geneteaud, responsable Marketing-Communication & Relation investisseurs de l’entreprise, parlent d’eux-mêmes : « d’un chiffre d’affaires de 372 M€ en mars 2018, nos objectifs sont d’atteindre 425 M€ en 2019, 520 M€ en 2020 et 650 M€ en 2023 ! ».
Une progression fulgurante au regard des chiffres de la société lotoise créée par Jean-Claude Maillard et qui est devenue en trente ans un sous-traitant de rang 1 pour les avionneurs, avec quatorze sites de production dans le monde. « À mon arrivée en 2000, nous n’étions que 120 salariés à Figeac contre environ 1 200 aujourd’hui », raconte Jean-Marie Morel, responsable Outils coupants de la BU « Structure ». Au total, l’effectif de cette entreprise créée en 1989 atteint aujourd’hui 3 300 salariés dans le monde dont environ 2 000 en France.
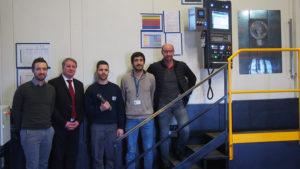
De gauche à droite : Grégory Lafon, Laurent Le Méteil, Lionel Coustillière, Baptiste Chevalier et Jean-Marie Morel
Des contraintes d’usinage liées à une explosion de la demande
Faire l’acquisition de sociétés aux savoir-faire techniques complémentaires tout en recrutant de nombreuses compétences en interne, ne suffit pas. Afin de répondre à « une explosion de la demande », pour reprendre les mots de Baptiste Chevalier, responsable Outils coupants de la BU « Moteurs », il faut adapter en permanence l’outil de production. Rien qu’à Figeac, une dizaine d’ateliers de production sont sortis de terre ces vingt dernières années ; avec un seul objectif : assurer la production de pièces et de sous-ensembles pour les grands programmes tels que l’A350 – fabrication de planchers et de pièces de mâts de réacteur – ou encore le Boeing 787 – fabrication de serrures et de mécanismes de portes,… « Nous travaillons essentiellement pour des avions de plus de cent places », précise Baptiste Chevalier. Outre les sous-ensembles, Figeac Aéro produit des pièces de structure telles que les longerons – soit des pièces de plus de 10 mètres de long et des nervures en titane pour rigidifier les longerons, des cadres, des rails de plancher, des carters de moteur, des pièces de trains d’atterrissage… la liste est longue et continue de s’étendre à mesure que le groupe engendre de nouveaux contrats, comme en novembre dernier avec MHI Canada Aérospace. Figeac Aéro produira des pièces et sous-ensembles pour le programme business jet Global Express de Bombardier.
On l’aura compris, produire des volumes croissants de pièces usinées en aluminium, en titane ou autres métaux durs implique de tout miser sur l’enlèvement de matière, tout en répondant à un niveau de qualité optimal. Une équation difficile à résoudre en production, d’autant, qu’en 2014, l’ancien fournisseur d’outils coupants présentait des incertitudes quant aux développements de ses produits. « En somme, nous n’étions pas sûrs que la technologie des futurs outils coupants serait capable de suivre celle de nos machines. Il fallait donc trouver un autre fournisseur ; nous ne pouvions pas prendre ce risque industriel », résume Jean-Marie Morel.
La priorité pour Figeac Aéro était de se doter d’outils coupants de pointe, capables de répondre à l’accélération de la production en intégrant des machines-outils. Celles-ci étaient désormais plus performantes (la puissance de broche est passée de 80 à 120 kW). Les anciennes gammes d’outils coupants étaient limitées à une vitesse de broche de 22 000 tr/min. Insuffisant pour Baptiste Chevalier ; « les nouvelles machines nécessitaient dès lors des outils capables d’opérer à 33 000 tr./min. De plus, une réflexion a été menée pour standardiser les outils coupants au niveau du site de Figeac, de façon à mieux rationaliser nos stocks, améliorer la disponibilité des outils et réduire les coûts ».
Le choix du groupe s’est orienté vers les outils Mitsubishi Materials. « Il fallait à tout prix que les outils fonctionnent sur des broches de 120 kW et sur nos porte-outils, mais aussi que l’entreprise soit capable de nous accompagner dans nos montées en production. En plus d’être une entreprise internationale, Mitsubishi Materials nous a proposé une solution répondant parfaitement à nos besoins ».
Un outil adapté pour relever les défis d’usinage
Le cœur de métier de Figeac Aéro, c’est l’usinage. Les équipes du groupe, réparties à travers plusieurs unités de production – une dédiée aux moteurs, une autre à l’aluminium, à la précision, aux métaux durs etc – savent précisément ce qu’elles veulent. En travaillant étroitement avec Laurent Le Méteil, responsable Business Aéronautique, et Grégory Lafon, technicien d’applications, tous deux chez MMC Metal France, elles ont pu tester une fraise entièrement dédiée à l’usinage à haute vitesse de pièces en aluminium, l’AXD4000. Qualifiée pour des vitesses de 35 000 tr./min (et jusqu’à 10 000 cm3/min. de débit copeaux), cette fraise a spécialement été développée au Japon en partenariat avec Makino, la marque des deux puissantes machines nouvellement installées dans l’atelier. « Grâce à ce développement commun, nous sommes parvenus à trouver le meilleur compromis entre les performances, la stabilité renforcée et la sécurité de l’outil, précise Grégory Lafon. Deux empreintes sur le corps d’outil et la plaquette ont été réalisées afin d’obtenir un système anti-éjection performant et un positionnement optimal. Une technologie qui permet aussi de réduire au minimum le saut de dents afin d’améliorer la durée de vie de l’outil et garantir un excellent état de surface de la pièce ».
Ce ne sont pas les seuls avantages de la fraise AXD4000. Les angles de ramping sont suffisamment agressifs pour optimiser les parcours outils et ainsi bénéficier d’un gain de temps non négligeable de l’usinage des pièces. Concernant la géométrie de l’outil, les poches à copeaux ont été dessinées de manière optimale afin de faciliter l’éjection du copeau et son évacuation tout en maintenant une rigidité accrue du corps d’outil. Enfin, et c’est un critère essentiel pour Figeac Aéro, le choix du diamètre de corps d’outils disponible de 20 à 125 mm comme le large éventail de rayons de plaquettes, allant de 0,4 mm à 5 mm. « Il s’agit d’un outil d’ébauche qui nous permet de standardiser un volume important de plaquettes du fait de sa durée de vie élevée, confirme Jean-Marie Morel. Nous avons pu ainsi réduire nos stocks et le nombre de références de plaquettes. Nous ne comptons désormais plus que deux géométries pour un seul et même outil. Celui-ci s’adapte autant aux nouvelles broches qu’aux anciennes ». Et Baptiste Chevalier d’ajouter : « nous n’avons eu qu’à mettre en lieu et place l’outil coupant ; l’encombrement initial a bien été respecté par l’équipe de Mitsubishi Materials. Globalement, les performances de la fraise AXD4000 nous ont permis de répondre à la forte hausse des volumes. Quant aux casses de plaquettes, elles ont fortement diminué et leur durée de vie s’est accrue d’environ 25% ».
Laurent Le Méteil ajoute que la deuxième phase du projet a permis à Mitsubishi Materials d’adapter les tourteaux pour l’ensemble de la gamme d’usinage. « Nous avons eu le feu vert du Japon pour fournir des fraises d’autres dimensions. Nous avons créé des plans spécifiques et adapté nos tolérances de diamètre d’outils pour les passer sur toutes les pièces de Figeac Aéro ». Un bel exemple de coopération qui va bien au-delà du simple échange client-fournisseur. Une relation de partenariat qui, dans tous les cas, doit s’imposer pour mener à bien un projet d’une telle envergure…
EQUIP’PROD • N° 105 Janvier 2019