Entrer de plain-pied dans l’ère de la modernité
SANDVIK COROMANT
parÀ l’occasion de son 75e anniversaire, le spécialiste des outils de coupe et des systèmes d’outillage nous a ouvert les portes de l’usine de Gimo, en Suède. Sandvik Coromant en a profité pour lever le voile sur un nouveau concept de tournage révolutionnaire : la méthodologie PrimeTurning et les outils associés. Ce nouveau concept constitue la première vraie solution de tournage dans toutes les directions ; les fabricants du secteur de l’aéronautique et de l’automobile l’apprécieront plus particulièrement.
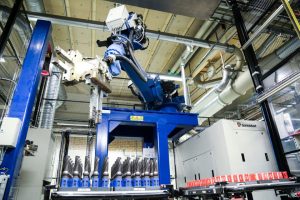
L’usine de Sandvik Coromant de Gimo associe l’automatisation à un savoir-faire de soixante-quinze ans
Cela ne fait aucun doute, nous sommes en Suède. Des dizaines de kilomètres de forêts de sapins au cœur desquels ondinent de nombreux lacs aux reflets bleus ; c’est dans ce décor que s’est érigée l’usine Sandvik Coromant. Implantée depuis 1951 à Gimo, une petite ville de 2 700 âmes située dans la municipalité d’Östhammar, l’entreprise regroupe 1500 salariés dont 900 opérateurs et pas moins de 600 ingénieurs. Véritable poumon du savoir-faire du premier carburier mondial, le site s’appuie sur d’importants moyens de production, depuis l’arrivée de la matière au conditionnement des millions d’unités sortant chaque année des lignes de production. Celles-ci totalisent environ 100 000 m2 de surface, nécessaires pour réaliser les célèbres outils de coupe, mais également pour fabriquer les propres machines de l’entreprise.
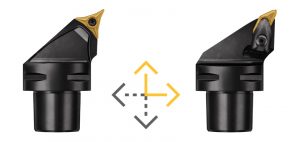
La nouvelle méthodologie PrimeTurning et les outils CoroTurn Prime type A (à gauche) et type B (à droite) permettent pour la première fois le tournage dans toutes les directions
L’usine de Gimo est pleinement associée à la modernité. Automatisation (avec notamment de nombreuses voies de circulation de chariots autonomes – AVG) et robotisation des moyens de production coïncident avec la démarche environnementale dans laquelle s’implique l’entreprise depuis plusieurs années déjà ; outre les fonctions « éco » équipant l’ensemble des machines et leur évitant toute consommation d’énergie inutile à partir de 60 minutes d’inactivité, l’énergie recueillie à partir des tours de refroidissement, des compresseurs d’air, de la ventilation des procédés et d’autres refroidisseurs à l’usine d’insertion est recyclée et utilisée pour chauffer ou refroidir l’immeuble.
Des mesures d’économie d’énergie telles que le montage de surchauffeurs sur les refroidisseurs et les ventilateurs dessiccateurs ont réduit de 46% la consommation totale de pétrole de Sandvik Coromant, de 2012 à 2016. L’eau d’un bassin externe est utilisée pour rincer les toilettes à l’usine d’outils, au lieu d’eau potable traitée. Enfin, notons que Sandvik Coromant récupère plus de 80% du carbure solide qu’il vend en collectant des inserts utilisés auprès des clients. L’entreprise utilise deux usines de recyclage certifiées ISO 14001 et OHSAS 18001 pour recycler les inserts ; au total, la production à partir de matériaux recyclés permet de réduire de près de 40% les émissions globales de dioxyde de carbone de l’entreprise.
Sandvik Coromant dévoile une révolution dans le tournage
Le site de Gimo repose aussi sur un centre d’excellence et de démonstration imposant, bien représentatif de la capacité d’innovation de l’entreprise, capable d’alimenter chaque année une offre pléthorique, au rythme de six nouveaux par jour ! Une performance qu’elle doit à un important centre de R&D ; des nouveautés produits mais également des innovations à part entière, à l’exemple de PrimeTurning, une méthodologie que le carburier définit comme « la première solution de tournage dans toutes les directions disponible dans l’industrie, et dont l’objectif est d’offrir une plus grande flexibilité pour l’usinage, la productivité et la durée de vie des outils ». Contrairement au tournage conventionnel qui est resté inchangé pendant des décennies, PrimeTurning autorise le chariotage en avant et en arrière, le dressage et le profilage avec un seul et même outil. La méthodologie est basée sur une entrée en coupe au niveau du mandrin et sur l’enlèvement de la matière en progressant vers l’extrémité de la pièce. Cette approche autorise l’emploi d’un petit angle d’attaque et permet d’appliquer des conditions de coupe plus élevées. En outre, les mêmes outils permettent aussi d’effectuer le tournage conventionnel (de l’extrémité de la pièce vers le mandrin).
Selon Sandvik Coromant, il serait possible d’obtenir un gain de productivité de plus de 50% dans certaines applications avec PrimeTurning par rapport au tournage conventionnel. Certaines de ces améliorations sont à attribuer au petit angle d’attaque qui crée des copeaux plus fins et larges et éloigne la charge et la chaleur du rayon de bec. En conséquence, les conditions de coupe et la durée de vie des outils sont accrues. Par ailleurs, comme le tournage s’effectue en s’éloignant de l’épaulement, il n’y a pas de risque de bourrage des copeaux (un problème courant et gênant dans le chariotage conventionnel). La productivité est favorisée par la meilleure exploitation des machines qui résulte des temps de montage réduits et des arrêts de la production moins fréquents pour les changements d’outils.
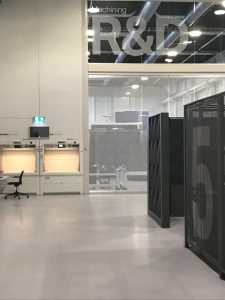
Chez Sandvik Coromant, la culture de R&D est depuis toujours la clé de voûte de la stratégie de l’entreprise
L’aéronautique et l’automobile en ligne de mire
PrimeTurning sera particulièrement apprécié dans les secteurs de l’aéronautique et de l’automobile qui effectuent des opérations de tournage en grandes séries et où des montages et des changements d’outils multiples sont souvent nécessaires. « Les opérateurs expérimentés savent qu’un petit angle d’attaque permet d’augmenter les avances, indique Håkan Ericksson, responsable de la technologie des applications chez Sandvik Coromant. Mais avec le tournage conventionnel, ils sont obligés d’utiliser des angles d’attaque d’environ 90° pour atteindre les épaulements et éviter les copeaux longs et enroulés caractéristiques des petits angles d’attaque. PrimeTurning résout ces problèmes en combinant un accès parfait aux épaulements et l’application d’angles d’attaque de 25-30° avec un excellent contrôle des copeaux et des tolérances régulières. Cette innovation offre une infinité de façons de réaliser les opérations de tournage de manière beaucoup plus efficace et productive. Il ne s’agit pas seulement d’un nouvel outil, c’est une nouvelle manière d’effectuer le tournage ».
PrimeTurning est lancé avec son générateur de code et deux outils spécifiques CoroTurn Prime ; le générateur de code PrimeTurning offre une programmation et des techniques optimisées. Les plaquettes CoroTurn Prime sont dotées de trois arêtes : une pour le chariotage, une pour le dressage et une pour le profilage, ce qui autorise une exploitation plus efficace de chaque arête et une durée de vie plus longue. Deux plaquettes spécifiques uniques sont proposées : CoroTurn Prime type A possède trois arêtes à 35° et est conçue pour l’ébauche légère, la finition et le profilage alors que CoroTurn Prime type B possède des arêtes très résistantes et est conçue pour l’usinage ébauche. Neuf plaquettes CoroTurn Prime type A et six plaquettes CoroTurn Prime type B adaptées aux matières ISO P (aciers), ISO S (superalliages réfractaires et titane) et ISO M (aciers inoxydables) sont actuellement disponibles ; de nouvelles plaquettes pour d’autres matières seront introduites ultérieurement. 52 variantes de porte-outils sont proposées, dont des versions Coromant Capto®, CoroTurn QS et à manche. Le générateur de code PrimeTurning offre à la fois une production maximum et des process fiables avec des avances adaptées et des rayons d’entrée optimaux. Il produit du code ISO compatible avec différents systèmes CNC.
N° 90 Juin 2017