De l’innovation à l’industrialisation automobile
MMC METAL FRANCE / SMP
parDepuis 1977 à Flers (Orne), la SMP fabrique des outils de presse pour la découpe et l’emboutissage. Aux avant-postes de la filière automobile, l’entreprise a consacré plusieurs années au développement de ses outillages destinés à l’emboutissage à chaud afin de les adapter à un process continu pour la fabrication de pièces de structures allégées. Le système de refroidissement (un des points clés), est entièrement percé dans la masse ; une opération complexe pour laquelle MMC Metal France s’est investie pas à pas aux côtés de son client afin de lui offrir un avantage décisif.
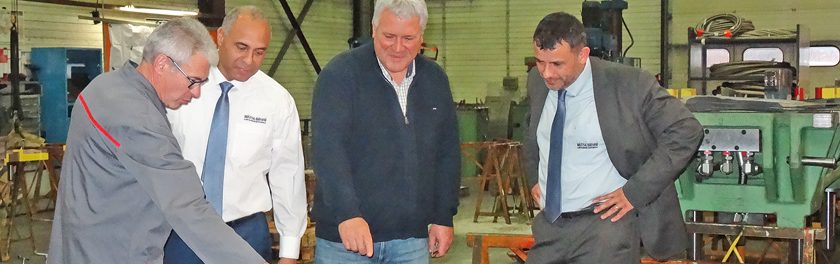
Alain Marteau, Fabrice Bouquety, Didier Lebarbier et Arnaud Panaget devant un outillage de presse destiné à l’emboutissage à chaud
Depuis qu’elle se consacre aux outillages de presse (pouvant atteindre 30 tonnes), l’usine SMP n’a cessé de s’agrandir pour être en mesure d’accueillir quarante-huit salariés. Cette croissance est liée à son offre technologique, constamment enrichie par une culture de l’amélioration continue et de l’innovation portée par le dirigeant et président, Didier Lebarbier, et son équipe. Cette passion commune pour leur métier en lien avec l’écoute qu’ils portent aux attentes de leurs clients est vitale dans le contexte très concurrentiel du secteur automobile. L’enjeu économique de l’outillage de presse pour un nouveau véhicule et son coût élevé de fabrication ne laissent pas de droit à l’erreur sur ce type de fabrication.
La recherche de gains dans la performance en usinage est à l’origine d’une collaboration vieille de plus de 10 années avec Mitsubishi Materials. À l’écoute de son client, Arnaud Panaget, technico-commercial chez MMC Metal France, visite régulièrement SMP et des propositions souvent ambitieuses prennent forme à la suite d’échanges avec Alain Marteau, chef d’atelier usinage. Dans leurs recherches d’amélioration continue des stratégies d’usinage, ils ont privilégié l’usage d’outils à haut rendement et à avance rapide, lorsque des gains significatifs pouvaient être obtenus.
La nécessité de relever des défis très techniques
Les constructeurs étant toujours plus attentifs aux objectifs de réduction du poids et de la consommation des véhicules, SMP s’est engagée avec son équipe, dès 2004, dans le développement de la technologie d’emboutissage à chaud et dans la fabrication de pièces automobiles – Le bénéfice étant d’augmenter la résistance et la sécurité des pièces de structure tout en diminuant le poids de ces éléments. De nombreuses difficultés sont à surmonter pour réaliser un outillage dédié à ce processus qui met en forme la pièce à plus de 600° et assure son refroidissement brutal à moins de 100°, telle une trempe thermique.
Dans le déploiement industriel de cette nouvelle fabrication, le forage de l’empreinte est une des opérations les plus délicates à maîtriser. L’ensemble poinçon-matrice comporte un réseau de circulation d’eau de refroidissement très dense au plus près des formes de la pièce. Un élément de petite taille (400x300x200) d’une empreinte comporte jusqu’à 78 perçages selon la complexité de sa forme. Parce qu’elle conditionne la qualité de fonctionnement du process d’emboutissage à chaud, la précision de positionnement des perçages profonds, dans n’importe quelle position angulaire, est un enjeu majeur sur les plans économique et technologique. Heureusement, l’expérience d’Alain Marteau a permis de progresser rapidement dans l’usinage et le perçage 5 axes des outillages. Les premières réalisations ont été effectuées avec des forets HSS, le temps d’évaluer tous les facteurs de difficultés à prendre en compte. L’implication d’un spécialiste outils pour l’optimisation de cette opération était une évidence pour le chef d’atelier. Celui-ci a mis à contribution Arnaud Panaget et Fabrice Bouquety le responsable régional MMC Metal France, lesquels sont ses partenaires Mitsubishi Materials.
Il convenait de trouver un procédé parfaitement étudié. Sélectionné pour ses caractéristiques mécaniques, l’acier de forge utilisé est un matériau reconnu pour être difficile à usiner par les fabricants d’outils. Sa structure particulière n’entre pas dans un modèle prédéfini, ce qui augmente les difficultés rencontrées dans le cas des perçages profonds débouchant en plusieurs endroits, avec des angles de faibles amplitudes. Pour Arnaud Panaget, il n’y avait pas de cas similaire sur lequel s’appuyer ; « avec cet acier un peu particulier, nous avions besoin de trouver des compromis pour bénéficier d’avances rapides, malgré les variations de contraintes, lorsque le foret traverse un conduit. Dans un objectif de productivité et de sécurité, j’ai retenu les forets carbure revêtus de la gamme MPS. Leurs larges goujures permettent une bonne évacuation des copeaux et le double listel assure la précision attendue, évitant tout aléa en cours de process. La performance de coupe et la longévité réputée de l’outil nous offrent un maximum d’amplitude pour affiner l’optimisation des temps de cycle et des coûts ».
Travailler main dans la main
Pendant un peu plus de six mois d’essais, l’opérateur, le chef d’atelier et son interlocuteur MMC Metal France ont établi les abaques de coupe à utiliser en fonction des stratégies d’usinage et des principaux forets à employer (L= 20 à 40xD). « La qualité de la coupe a été notre fil conducteur pour établir une grille des vitesses et avances pour le perçage sur de grandes profondeurs, explique Alain Marteau. Notre premier indicateur visuel était la qualité du copeau obtenu. Sa forme en coquillette servait de juge de paix pour cadrer les limites d’utilisation (avance) ». La longueur cumulée de tous les perçages d’un outillage complet d’emboutissage à chaud donne une idée de l’importance stratégique des opérations de perçage en 5 axes dans le challenge engagé par SMP. Travaillant main dans la main pour analyser le travail accompli, le duo a réussi à diviser plusieurs fois les temps de cycle. « Nous avons dû tester un certain nombre d’outils pour définir nos paramètres de vitesse et d’avance continue, confie le chef d’atelier. L’engagement d’Arnaud Panaget a libéré nos craintes. Plus d’une fois il nous a fourni des outils pour aller au bout de nos essais. Ce partenariat a débouché sur l’acquisition d’un véritable savoir-faire ».
Au-delà de la complicité des personnes, la confiance réciproque établie entre les partenaires a fait progresser les deux entreprises. Les attentes que le client porte sur l’outil idéal trouvent écho chez Mitsubishi Materials : le foret MPS L= 40xD est devenu un standard catalogue et au-delà même, jusqu’à sa version 70XD réalisable à la demande. Alain Marteau a eu l’opportunité de se rendre sur le site du M-VEC en Espagne. Cette usine Mitsubishi Materials située près de Valence est aussi le centre européen d’essais et de formation de la marque. « J’ai pu observer la façon dont les forets MPS usagés étaient reconfigurés à neuf, constate Alain Marteau. L’affûtage de l’arête et l’installation du revêtement anti-usure prolongent jusqu’à 7 fois la durée de vie de nos outils, pour un coût bien inférieur à celui de l’utilisation d’un outil HSS équivalent ».
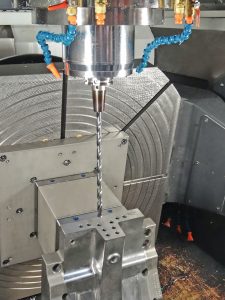
Le foret MPS permet les perçages longs pour réaliser le circuit de refroidissement de l’ensemble poinçon-matrice
En quelques années d’investissements lourds, avec notamment deux centres d’usinage 5 axes permettant de réaliser des forages profonds, une presse à chaud et son four pour les essais et préséries, Didier Lebarbier a donné une forte impulsion à son entreprise et tire satisfaction de son pari d’entrepreneur. Il dispose d’un avantage concurrentiel certain dans un marché où chaque véhicule se distingue par la surenchère technologique qu’il propose. Les équipementiers emboutisseurs ont adopté cette technologie novatrice. L’emboutissage à chaud représente déjà 50% de l’activité de SMP et MMC Metal France poursuit l’accompagnement de son client dans son évolution technologique. De nouvelles solutions d’outillage, élaborées avec le soutien technique des experts de l’usine européenne de Mitsubishi Materials, sont déjà en cours de développement.
N° 87 Mars/Avril 2017