À pleines dents, ADC modèle le futur
MMC Metal France / ADC
parJacques Pinto a tout de suite pris la mesure des compétences peu communes d’ADC pour l’usinage de prototypes complexes. À la recherche d’une PME de mécanique de précision disposant d’un réel potentiel à développer, il a saisi l’opportunité de se porter acquéreur d’ADC en 2015. Animé par ce challenge, le nouveau dirigeant n’a cessé de renforcer son partenariat avec MMC Metal France, qui s’est révélé être un fournisseur stratégique pour le développement de son entreprise.
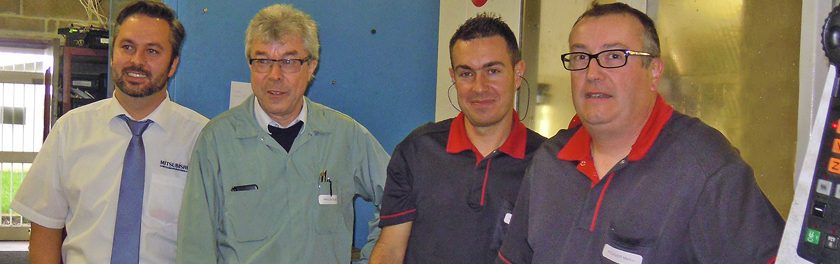
G.Bouet (responsable régional de MMC Metal France), J.Pinto (président d’ADC), Sébastien et Martial (technicien/régleur ADC)
Les entreprises phares de l’aéronautique, de l’automobile de compétition, et de bien d’autres secteurs comme l’agroalimentaire, font appel aux Ateliers des Commanderies (ADC) pour le prototypage en vue d’affiner la conception des produits et leur industrialisation. Ceci a conduit les opérateurs à se familiariser très tôt avec la complexité de process toujours plus innovants. Aujourd’hui, la société rassemble une équipe de 24 spécialistes disposant d’un parc de 25 machines CNC (dont 6 machines 5 axes) associé à une FAO version X 10, avec la certification EN9100 en cours.
Parce que l’atelier est naturellement orienté vers les nouveaux produits, l’usinage des prototypes est effectué le plus souvent à partir d’un bloc de matière technique : des métaux réfractaires (titane, inconel…), difficiles (composites, inox,…) ou tendres tels que les cupro, l’aluminium… De l’ébauche dans la masse à la finition, l’opérateur doit faire preuve d’une grande agilité pour définir des stratégies d’usinage qui prennent en compte la complexité des formes, la précision géométrique et la qualité de surface à respecter. Toutes les garanties pour réussir la pièce du premier coup reposent sur sa compétence. Il doit produire à moindre coût, sans tâtonnement et connaît les enjeux de son travail en cas de non-conformité : un rachat de matière, du retard pour le client, des coûts élevés pour une nouvelle fabrication…
Un partenaire outils de longue date
Dès sa création en 1990, l’entreprise ADC s’est spécialisée dans l’usinage 5 axes, affirmant sa vocation de pionnier dans un environnement de haute technologie, avec une compétence rare pour l’époque et très recherchée dans le domaine des prototypes, tous secteurs d’activité confondus. Grégory Bouet, responsable régional MMC Metal France, rendait régulièrement visite aux responsables ateliers d’ADC, mettant en avant les qualités et les performances d’une gamme d’outils bien adaptés aux travaux de son client. En 2012, avec la participation de Sébastien, technicien/régleur ADC, très impliqué dans les réalisations de pièces complexes, une étape décisive a été franchie. En première ligne sur les fabrications difficiles, il partageait la même ambition que son partenaire MMC Metal France : démontrer l’importance du choix de l’outil dans les productions quasi unitaires. « Les bonnes machines sont vite limitées pour les travaux les plus délicats si elles ne sont pas équipées des meilleurs outils ». Ensemble, ils ont élaboré un process de contournage de forte profondeur avec la fraise Mitsubishi Materials VQ – diamètre de 16mm – dotée d’un revêtement très résistant pour l’ébauche d’une pièce de grande taille en inox 304 L. Précédemment, cette opération s’effectuait avec une fraise ravageuse travaillant en mode rainurage avec des avances réduites. Malgré ces paramètres modérés, la consommation d’outils était significative.
En suivant les recommandations proposées par MMC Metal France, l’équipe d’ADC a pu doubler les vitesses de coupe et d’avance de l’outil, malgré une profondeur de coupe de 16 mm contre 3 précédemment. La qualité d’usinage, la baisse exceptionnelle des temps machines et la longévité de l’outil améliorée de 50% ont attesté de la fiabilité et de la rentabilité économique d’outils bien conçus. Cette évaluation comparative a stimulé l’intérêt des opérateurs pour la reproduction de cette stratégie d’usinage sur de nombreuses applications et servi de déclic en créant une attitude d’exigence concernant le choix du bon outil utilisé avec les meilleurs paramètres d’usinage.
Maintenir un niveau maximal de technicité
Attentif aux évolutions de sa structure, le dirigeant d’ADC est également un promoteur engagé du partenariat avec l’équipe MMC Metal, Mitsubishi Materials en France. « Quand on fait le choix d’investir sur un capital humain et des machines high-tech, on se doit de libérer la performance et favoriser ce qui rapporte ». S’il connaît bien son fournisseur et l’ensemble des fabricants d’outils à la suite d’une belle carrière dans la machine-outil, Jacques Pinto se positionne avant tout selon les axes qu’il a définis pour faire progresser son entreprise. « Nos clients attendent de notre part un degré de technicité qui va jusqu’aux limites du réalisable, si cela s’avère nécessaire. C’est un avantage stratégique qui leur est indispensable pour le développement de leur produit. C’est également vrai dans le domaine de la compétition. A cela, il faut ajouter leurs impératifs de planning et l’on sait que pour développer un produit, le mettre au point parfaitement, il faut souvent revoir plusieurs fois sa copie. Pour eux, le temps, c’est de l’argent. Concernant notre partenariat avec Mitsubishi Materials, nous avons les mêmes attentes que nos clients. Nous raisonnons en mode projet pour réfléchir en amont sur ce qui est déterminant dans le process d’obtention d’une pièce. Faut-il un outil sur mesure, quels paramètres de coupe envisager ? Par sa disponibilité, son écoute et les solutions qu’il propose, Grégory Bouet a su gagner la confiance des opérateurs. Avec lui nous mettons toutes les chances de notre côté pour sécuriser une production en veillant à minimiser son coût. Mitsubishi Materials fait évoluer ses gammes d’outils afin d’augmenter leur performance et cela nous permet d’être en pointe dans notre métier ».
Cette priorité accordée à la performance et à la réactivité voulues par Jacques Pinto s’inscrit dans le quotidien des relations avec Mitsubishi Materials. En concertation avec les équipes ADC, le conseiller MMC Metal France veille à garantir la disponibilité des outils par une bonne anticipation des besoins futurs. A chaque nouveau projet, le savoir-faire des opérateurs est confronté à de nouveaux challenges : une accessibilité des usinages, des tolérances de géométrie, un état de surface et une précision auxquels il faut ajouter les paramètres d’usinabilité de matériaux innovants. La réactivité de Grégory Bouet est un appui technique particulièrement apprécié pour maîtriser ces situations nouvelles dans un process à flux tendu. Ce qui est sûr, c’est qu’au pied des machines les compagnons passionnés par les solutions innovantes apprennent vite. « Avec nos équipements et outils nous pouvons atteindre des précisions de quelques microns avec une répétabilité sur des séries de 10 à 20 pièces et un état de surface qui nous évite de recourir à une opération de superfinition », assure Sébastien. A ses côtés, Martial, technicien/régleur ADC, ne tarit pas d’exemples pour illustrer les gains obtenus avec les différents outils Mitsubishi Materials : « nous avons ramené de 1 h30 à seulement 19 minutes le dressage et la finition d’un plat sur une pièce de très grande dureté avec une fraise anti-vibration VQ. Sur les travaux fins et précis, nous sommes tout autant en sécurité grâce aux outils de petit diamètre (0,2 mm) qui sont d’une rigidité sans équivalent ». Les Ateliers des Commanderies ont bien l’intention de continuer sur cette voie, aux avant-postes de l’industrie tournée vers le futur, à la recherche permanente de solutions évoluées et à la conquête de nouveaux clients.
N° 86 mars 2017