Usinage de haute précision de pièces complexes ouvragées et à parois minces
ROEDERS / CARL ZEISS
parCarl Zeiss à Oberkochen est convaincu des avantages du fraisage UGV pour la production de supports de structures cinématiques d’optiques de précision en petites séries. Obtenir les plus grandes précisions est ici une nécessité tant pour les usinages classiques que pour les formes complexes et dans des matériaux aussi bien tendres que durs, en UGV ; des exigences entièrement satisfaites avec la Roeders 5 axes RXP500DS.
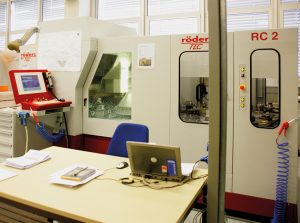
La Roeders 5 axes RXP 500 DS a été choisie en raison notamment de ses moteurs à commandes linéaires à la fois dynamiques et précis
«Nos produits méritent vraiment le label “haute technologie” ; bon nombre d’entre eux sont en service au-dessus de nos têtes, aussi bien dans le spatial que dans l’aéronautique », indique Alfred Langer, chef du département fabrication Produits spéciaux – établissement Carl Zeiss d’Oberkochen. En plus de produire les pièces mécaniques complexes, sa division réalise des solutions haut de gamme dans le domaine des composants optiques et des assemblages sophistiqués. Grâce aux liens étroits entre le département interne de conception et le département R&D, les clients peuvent bénéficier d’un support dès les premières étapes de la conception de nouveaux produits. Carl Zeiss, leader sur le marché de la technologie dans les domaines de l’optique et de l’optoélectronique, dont les produits et services sont largement utilisés dans la recherche biologique et médicale et dans la technologie médicale, développe également des solutions « clé en main » pour les industries du semi-conducteur, de l’automobile et de la construction de machines.
Beaucoup de ces produits à l’extrême pointe de la technologie sont réalisés à l’unité ou en très petite série, avec des produits connexes tels que les supports, cadres et mécanismes et avec les plus hautes exigences en termes de qualité et de précision. Le département exploite actuellement environ 25 machines-outils, principalement des machines à commandes numériques de pointe en tournage et de centres de fraisage en 3 ou 5 axes.
Ce large éventail d’applications conduit à usiner une gamme de matériaux variés qui vont non seulement des matériaux standard tels que l’aluminium, le carbone ou les aciers fortement alliés, mais aussi de nombreux matériaux « exotiques » présentant des propriétés physiques particulières, dont des matériaux très durs ou extrêmement difficiles à usiner. Étant donné que la société conduit souvent de tels projets avec des partenaires tant au niveau national qu’international, une part importante de commandes provient de clients externes.
Avantages du fraisage UGV
« Beaucoup des pièces de structure que nous fabriquons sont très ouvragées et à parois minces, telles que les structures porteuses d’optiques de précision, ajoute Richard Kaak, chef de projet en développement des technologies en ingénierie des procédés. Les efforts exercés par l’outil coupant peuvent conduire à la déformation de la structure et altérer la précision de la pièce ». Bien sûr, on pourrait théoriquement essayer de régler ce problème en réduisant drastiquement les vitesses de coupe, mais cette solution ferait non seulement monter en flèche les coûts d’usinage et elle conduirait à des retards inadmissibles dans les projets. Il convenait également de traiter en priorité d’autres problèmes tels que la correspondance entre les vibrations induites par l’usinage avec les fréquences propres des structures, et l’échauffement des pièces qui pouvaient entraîner des dispersions dimensionnelles.
Pour ces trois domaines problématiques, des améliorations sensibles étaient attendues en passant du fraisage conventionnel à l’UGV, caractérisé par la formation et l’enlèvement rapide des copeaux, des efforts de coupe plus faibles et des gammes de fréquences de vibration plus élevées induites par les grandes vitesses de rotation de la broche. Autre aspect important de la décision : l’efficacité économique. Même dans ce segment de marché hautement spécialisé, les coûts sont un facteur important et les décisions finales sont rarement prises par les techniciens seuls : les projets sont étroitement discutés avec le service achats.
Processus de sélection approfondi
« Avant de prendre une décision définitive, nous sommes passés par une phase d’évaluation très complète », rappelle Alfred Langer. Une recherche exhaustive de tous les fabricants potentiels du marché qui a rapidement conduit à la sélection d’une poignée de fournisseurs. Une matrice d’évaluation a ensuite permis une comparaison plus poussée. L’étape décisive suivante a été l’usinage d’une pièce test comportant toutes les complexités que Carl Zeiss voulait voir maîtriser. Le choix final, en faveur de la Roeders 5 axes RXP 500 DS, a été alors pris sur la base de ses moteurs à commandes linéaires à la fois très dynamiques et extrêmement précis, en association avec la rigidité de la machine.
La broche de 42 000 t/mn en HSK 40 dispose d’une puissance nominale de 14 kW. Un système de position-mesure à haute résolution, une gestion poussée de la température (refroidissement par plus de dix circuits dont une chemise autour de la broche), la détection et la compensation de la longueur de la broche assurent l’obtention des plus grandes précisions. Le nettoyage de l’outil avant mesure, le circuit de contrôle de température du liquide d’arrosage, le palpeur de mesure par point de contact et le laser de mesure de haute précision des outils sont autant de points forts pour assurer les précisions demandées.
Une des particularités de la machine est la correction automatique du point pivot de la table et du berceau en s’appuyant sur la mesure de points de référence répartis dans le volume de travail. Le système calcule les valeurs de corrections permettant d’obtenir les meilleures précisions que ce soit en 5 axes positionnés ou continus, sans aucune intervention de l’opérateur. « Avec ces fonctionnalités, la machine de Roeders obtient des précisions exceptionnelles sur tous les axes en relation avec l’usinage UGV. C’était exactement ce que nous recherchions », récapitule Alfred Langer.
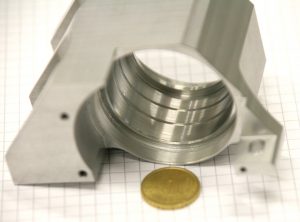
Beaucoup des pièces de structure fabriquées sont très ouvragées et à parois minces, telles que les structures porteuses d’optiques de précision
Des performances record
« Après une année et demi d’exploitation du système, nous pouvons maintenant déclarer que nos espoirs ont été comblés en ce qui concerne tous les besoins essentiels », affirme Richard Kaak. Ceci s’applique tant aux précisions obtenues qu’aux vitesses d’usinage. Pour donner un exemple, dans le cas d’un réceptacle complexe comportant plusieurs ajustements cylindrique de précision dont les axes doivent être alignées avec une grande précision, il est possible d’obtenir, en toute fiabilité, une précision de 5μm tant pour la position des axes que pour celle du calibre intérieur tout en assurant des circularités ne dépassant pas les 2μm. Un autre exemple est un anneau d’entretoise en filigrane avec les surfaces coniques dont les axes ont un angle d’inclination relatif de 5.3°. La tolérance de position pour le point d’intersection de ces axes – localisés loin à l’extérieur de la pièce elle-même – n’est que de 0,02 millimètres.
Il convient aussi de souligner les niveaux de précision obtenus en 5 axes qui, avec les mesures sophistiquées des déviations internes et les fonctionnalités de compensation de l’armoire, permettent des niveaux de précisions qui surpassent parfois ceux obtenus autrefois avec les technologies employées dans le département. Une autre fonctionnalité remarquable de la Roeders est son équipement d’automation qui lui permet de travailler la nuit, sans surveillance. Le changeur de palettes de 18 places et le changeur d’outils de 100 places ont ainsi considérablement contribué à réduire les coûts.
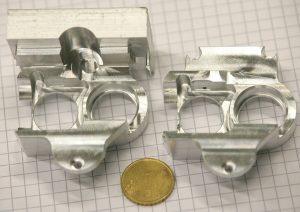
› En plus des pièces mécaniques complexes, cette division de Carl Zeiss réalise des solutions optiques haut de gamme et des assemblages sophistiqués
Le support : « poste décisif du package global »
« Un autre facteur majeur réside dans l’excellent support obtenu du fabricant de système », explique Alfred Langer. C’était le plus important puisqu’avec l’achat du nouveau centre d’usinage, la société entrait dans un territoire inexploré avec le système de contrôle propre à Roeders. Cependant, ce système de contrôle spécifiquement développé sur une base PC et soigneusement optimisé par le fabricant lui-même, pour correspondre exactement à son matériel d’usinage, était plutôt convaincant.
Dans ce contexte, la facilité avec laquelle le système de contrôle pouvait être mis à jour était très intéressante. En effet, l’installation et l’utilisation d’améliorations ou de fonctions spéciales que Roeders a partiellement développées sur mesure pour Carl Zeiss, étaient immédiatement disponibles après leur réalisation et simplement installées à partir d’un CDRom. Dans tous les cas, le support de Roeders s’est avéré déterminant, tout autant que la qualité de leurs services techniques.
Des avantages le long de la chaîne de réalisation
« Autres points remarquables : ce sont les avantages supplémentaires que nous avons découverts tout au long de la chaîne de production », explique Richard Kaak. La grande précision d’usinage réduit de manière significative les coûts pour les étapes suivantes du processus, telles que l’ébavurage et le polissage.
En outre, il est maintenant devenu plus facile d’éviter de recourir au moulage comme technologie de production alternative. Dans le passé, ceci s’avérait souvent inévitable dans la mesure où plusieurs des composants ont des parois si minces qu’elles n’auraient pas pu résister aux efforts d’usinage exercés avec une technologie de fraisage conventionnel. De plus, avec le moulage, un certain niveau d’opérations d’usinage demeurait nécessaire, par exemple dans le cas d’ajustements précis et des surfaces d’étanchéité. Un autre inconvénient était que ces surfaces moulées ne peuvent pas être anodisées avec un niveau de qualité suffisant. En basculant à l’UGV, les forces exercées sur la pièce sont considérablement réduites et cela procure même de nouvelles opportunités de faire appel aux techniques de fraisage.
Traduction P. Marquant –
article Roeders de K. Vollrath
N°91 Septembre 2017