Une solution d’usinage complète et robotisée pour une application inédite !
HURCO / TCT
parDans le domaine de la mécanique générale, un fabricant de machine peut s’ouvrir une multitude de possibilités d’applications, parfois éloignées de ce qu’il aurait pu imaginer. C’est le cas d’Hurco qui a mené un projet à la fois atypique et complexe pour TCT (Tores Composants Technologies), une société du groupe Socomec implantée dans la Nièvre et spécialisée dans la production de noyaux magnétiques et de composants passifs bobinés.
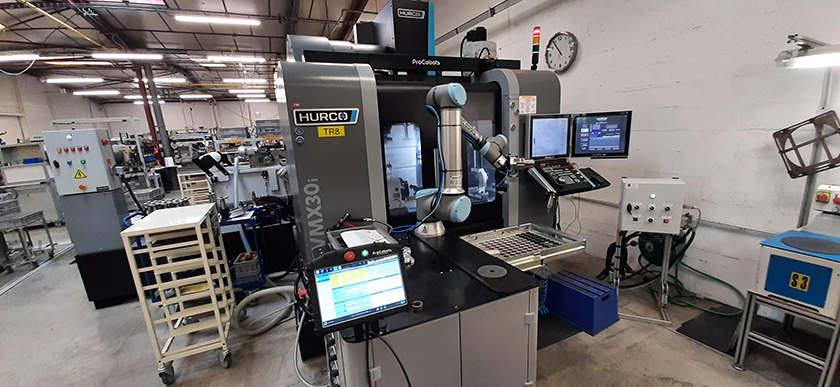
>> Vue de l’ensemble de la solution composée d’un centre 4 axes Hurco VMX30i et d’une cellule cobotisée ProCobots avec un bras Universal Robot
Qu’est-ce qui a bien pu amener une entreprise comme TCT, plus habituée à travailler avec des machines de découpe qu’avec des centres d’usinage, à s’adresser à un fabricant tel qu’Hurco ? « Notre équipe commerciale a reçu une sollicitation via notre site Internet car TCT rencontrait des limites dans la découpe de ferrites destinées à fabriquer ensuite des pinces ampèremétriques chargées de mesurer le courant qui passe dans un câble », résume Philippe Chevalier, directeur de la filiale française d’Hurco.
Cette opération est complexe pour TCT. Le process lui impose en effet d’empiler six pièces (des ferrites) sur un montage puis de générer la découpe via un disque abrasif. La ferrite en question, créée à partir d’un feuillard, est ensuite vernie, posant un problème de formation de bulles. Or, il est impératif d’obtenir une surface qui soit la plus plane possible, afin d’assurer une coupe parfaite et de maintenir ainsi le niveau de qualité optimale requis pour la fabrication des pinces. Il fallait donc trouver une autre solution permettant de garantir un process fiable et répétable, donnant en outre la possibilité pour TCT de monter en cadences… et de passer de 50 000 à 120 000 pinces ampèremétriques produites chaque année.
Plus qu’une machine, une solution complète mettant en scène plusieurs partenaires
De plus en plus souvent, les fournisseurs de technologies n’affirment plus proposer un produit mais une solution, complète si possible. Dans le cadre de ce projet, c’est pleinement le cas. Ne connaissant pas les métiers de l’usinage, TCT a demandé à Hurco de prendre le problème à bras le corps et de le résoudre. Comment ? « Au départ, nous avions suggéré une première solution à partir d’un centre 4-5 axes assisté d’un robot cartésien mais nous avons finalement opté pour un centre 3 axes équipé d’un plateau diviseur pour un 4e axe, de contre-paliers, d’un montage de bridage composé de sauterelles hydrauliques, d’un cobot et d’une station de chargement à tiroirs ».
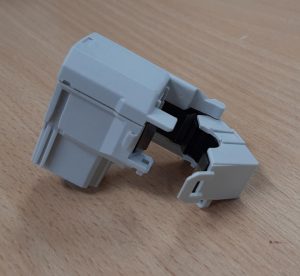
>> Pince ampèremétrique destinée à mesurer le courant dans un câble, pour diverses applications comme le suivi de la consommation électrique d’une usine
Concrètement, le cobot composé d’une pince de préhension servo et d’un préhenseur magnétique prend la ferrite et la pose dans le montage, les sauterelles brident la pièce et envoient les informations à la commande numérique pour effectuer la rotation du diviseur (4e axe) qui positionne l’outil venant couper la pièce en deux. Puis le robot récupère les deux pièces coupées à l’aide du préhenseur magnétique. Inédite pour l’entreprise, cette solution a pleinement trouvé sa place dans l’atelier et a convaincu les opérateurs et opératrices ; particulièrement motivés et ouverts à la nouveauté, « ils ont su créer une réelle dynamique et ont fait en sorte que ce beau projet réussisse », ajoute Philippe Chevalier.
Cette solution packagée est le fruit d’une entière collaboration entre Hurco France et TCT bien sûr, mais pas seulement. « Nos partenaires sont multiples : notre filiale ProCobots utilise un robot collaboratif d’Universal Robot. Pour le système de bridage, nous avons fait appel à ACS mais aussi à SCHUNK pour la partie préhenseur magnétique ; il faut dire que le process est particulier : on vient charger dans la machine une pièce qui est ensuite coupée en deux. Quant à la partie filtration, élément également important du process, elle était du ressort de Novaxess ».
Enfin, ce projet était une nouvelle fois l’occasion de faire interagir et travailler ensemble la filiale française d’Hurco avec le siège du groupe aux États-Unis sur un même projet, en particulier sur la partie robotique afin de l’alimenter en précieux retours d’expérience… pour d’autres défis à relever prochainement.
Olivier Guillon
EQUIP PROD • N°139 Octobre 2022