Un parc machines neuf au service de l’enseignement
Hurco - Ensam
parQui a dit que les établissements publics ne formaient plus les ingénieurs en mécanique sur des machines modernes ? Voilà une question à laquelle l’école des Arts et Métiers de Bordeaux-Talence répond avec une efficacité remarquable. Après avoir levé pas moins de 3M€ pour s’équiper de machines dernier cri, elle a notamment investi dans trois tours et quatre centres d’usinage Hurco pour former les futurs diplômés à l’usinage et ouvrir l’école aux industriels de l’aéronautique.
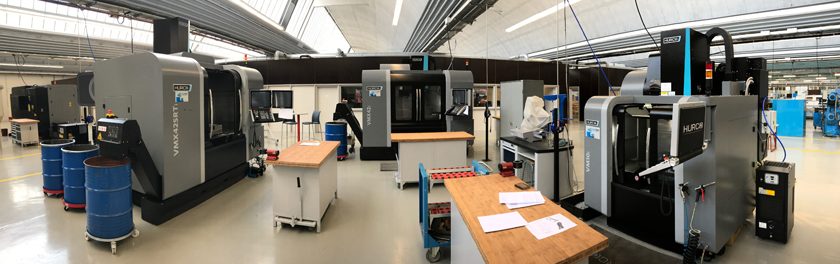
L’atelier d’usinage est composé de sept machines Hurco, trois tours (2, 3 et 4 axes) et quatre centres d’usinage (3 et 5 axes)
Un atelier d’usinage flambant neuf. Voilà ce qui frappe au moment où l’on pénètre dans ce hall de 8 400 m2 réparti en plusieurs îlots, allant de l’usinage au formage en passant par la découpe de tôle. Si, au départ, l’idée venait d’une simple modernisation de l’atelier, le directeur de l’école, Philippe Viot, s’est attelé à convaincre l’ensemble des membres de l’établissement ainsi que les principaux partenaires financiers, que sont la région Nouvelle-Aquitaine et quelques industriels, de l’intérêt d’un projet qui va bien au-delà de l’achat de quelques machines. Au niveau de l’esprit du projet tout d’abord, comme l’explique le directeur, « nous souhaitions mettre en place un système ouvert, à la fois aux étudiants de l’école mais aussi aux élèves de BTS et d’autres établissements qui n’ont pas accès à autant de technologies. Ensuite, l’idée consiste à travailler plus étroitement avec les industriels ».
Cet atelier entièrement refait à neuf, loin d’être un simple showroom, doit contribuer à former un écosystème permettant à tous les étudiants de se projeter dans un contexte industriel et aux entreprises, de la PMI aux grands groupes comme Hurco, de montrer leur savoir-faire. « Il faut voir cet espace de façon plus large, avec pour objectif la redynamisation de l’emploi industriel sur le territoire, notamment dans les secteurs de la mécanique dominés par l’énergie et l’aéronautique ».
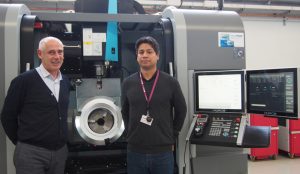
À gauche, Philippe Chevalier (Hurco) et à droite, Israel Robles, chef d’atelier et responsable de l’usinage
L’aéronautique comme cheval de bataille
Que l’on se trouve autour de l’agglomération bordelaise, dans la pointe sud-ouest de la France, ou plus au nord en Poitou-Charentes, les sous-traitants de l’aéronautique et du spatial sont nombreux et expriment, comme partout ailleurs, d’importants besoins de recrutements. C’est l’une des raisons pour lesquelles l’ENSAM de Bordeaux-Talence est fortement teinté d’aéronautique. Pour rappel, l’École nationale des Arts et Métiers se compose de huit campus répartis sur l’ensemble du territoire français et rassemble pas moins de 6 500 étudiants.
La modernisation de l’atelier de l’établissement bordelais, sur les terres de Dassault Aviation et au cœur du pôle Aerospace Valley, non loin de l’IRT St-Exupéry, permet aux étudiants de mieux entrer en contact avec les industriels. « Notre projet était avant tout d’ouvrir l’école d’ingénieurs vers l’extérieur, de faciliter les échanges tant au niveau des stages ou de l’emploi qu’à celui du transfert industriel », rappelle Philippe Viot. Pour ce faire, il était nécessaire de disposer d’équipements modernes tels qu’il en existe réellement dans les ateliers de production, à commandes numériques tactiles, dotés de logiciels actuels, aussi bien pour l’usinage que pour la découpe et la déformation plastique sans oublier la fabrication additive dont les moyens vont de 500€ à 100 000€ ! Les machines de tôlerie, à commencer par un impressionnant Laser Fibre Amada, trônent aux côtés d’une machine de découpe jet d’eau. Plus loin, s’opère la livraison d’une machine de fabrication additive avec un robot Kuka muni d’une tête laser pour la production de grandes pièces (jusqu’à 1,50 m.). L’atelier d’usinage est, quant à lui, composé de sept machines Hurco, de trois tours (2, 3 et 4 axes) et de quatre centres d’usinage : deux machines 3 axes équipées d’un diviseur pour le 4e axe et deux 5 axes, l’un de type SR doté d’une électrobroche pivotante et d’un plateau rotatif, l’autre d’une broche fonctionnant à des vitesses atteignant 18 000 tr/min.
Un large panel permet d’aborder la réalisation de pièces dans l’aéronautique, de toutes les manières et sur toutes les matières ; au dos d’un des centres Hurco 5 axes ont été intégrés un système d’aspiration avec filtration d’air à 25 microns et un système automatique de décolmatage : « cet équipement permet de travailler toutes les matières y compris les pièces en matériaux composites », souligne Philippe Chevalier, directeur d’Hurco France.
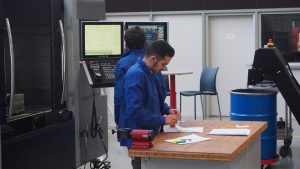
L’atelier « high tech » bordelais entend répondre à sa manière au problèmes de recrutements dans l’industrie, notamment dans l’aéronautique
Un investissement de taille dans l’usinage
Très clairement, le projet a pu arriver à son terme en mois de deux ans. Plus précisément, « il a commencé à germer à l’automne 2014, précise Philippe Viot. Après avoir eu le feu vert de la région Nouvelle-Aquitaine en juin 2015 puis défini le budget début 2016, nous avons pu lancer un appel d’offres. C’est en juin 2016 que nous avons fait l’acquisition de nos machines Hurco ». Ainsi, il a fallu moins d’une année entre le soutien officiel des partenaires institutionnels et le démarrage des opérations ; « dès la réception des machines, nous démarrions immédiatement le travail avec nos élèves, notamment des opérations d’usinage de pièces pour l’aéronautique ».
Il faut dire qu’avec des investissements de 3 M€ sur des machines d’usinage et de chaudronnerie aéronautique et des investissements machines majeurs en fabrication additive (1,2M€ en fabrication additive métallique sur le projet FuturProd, 1,4M€ dans le projet Ocean également sur l’impression 3D…), les étudiants ne peuvent qu’être enthousiasmés à l’idée de travailler sur des équipements neufs. « A la rentrée de septembre 2016, le plateau industriel a impressionné tout le monde, avec un changement profond de l’image que nos élèves, nos personnels et nos partenaires se font de l’industrie », se rappelle le directeur de l’ENSAM de Bordeaux-Talence. C’est le cas notamment des quatre robots (deux cobots) et des machines-outils ; un cobot est même en phase d’intégration à un tour Hurco.
Toutes ces machines bénéficient de leur propre post-processeur capable de recevoir des programmes sur Catia ainsi que la dernière génération de commande WinMax. L’ergonomie de la commande numérique n’est pas son unique point fort : « l’interface graphique Hurco est conviviale et tactile et nous avons la possibilité de travailler sur deux écrans, ce qui offre une vision globale sur tout ce qui se passe, de la géométrie de la pièce à la trajectoire en passant par les modifications apportées, témoigne Frédéric Lalardie, ingénieur d’études en fabrication mécanique et enseignant. « La vitesse de broche de 18 000 tr/min et les importantes avances d’outils nous permettent de montrer aux élèves ce que sont la productivité et la réalité industrielle. De plus, il leur est possible de réaliser des pièces de plus en plus complexes. Par exemple, nous mettions auparavant quatre heures pour produire une pièce relativement simple contre trois heures aujourd’hui pour des pièces que nous ne pouvions envisager de fabriquer auparavant ; au-delà du gain de temps, nous avons surtout pu complexifier le programme d’usinage ».
De leur côté, les étudiants sont unanimes : « nous avions déjà travaillé sur des CN – après avoir démarré sur du conventionnel pour étudier les rudiments de la coupe. Avec ces nouveaux tours et centres d’usinage Hurco, c’est tout de suite plus rapide et plus performant », affirme Bryan. Florian se montre lui aussi très enthousiaste, notant au passage, qu’outre l’interface graphique agréable et intuitive, « travailler sur de telles machines est très gratifiant ». Et comme chacun le sait : ce qui est gratifiant est également attractif. En ce sens, on peut dire que le premier objectif du projet est atteint ; il ne reste plus aux industriels et à l’ENSAM qu’à travailler de plus en plus étroitement afin de répondre aux besoins de recrutements.
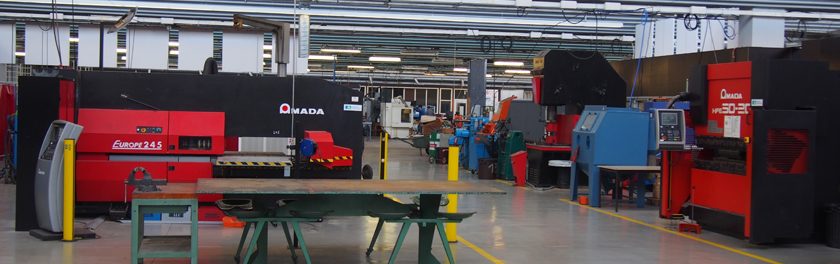
Les investissements de l’école ne se limitent pas à l’usinage comme en témoigne la partie consacrée à la tôlerie
N° 84 Février 2017