Un centre d’usinage 5 axes de haute précision pour une fabrication flexible de roues dentées
RÖDERS
parLa fabrication de roues dentées destinées au secteur de la construction mécanique est généralement effectuée sur des machines spécifiquement conçues pour cet usage. Alors que les principales méthodes (taillage, mortaisage, rabotage, fraisage et brochage de profils…) nécessitent des outils spéciaux et plusieurs étapes, Röders a développé des centres d’usinage universels 5 axes permettant de fabriquer rapidement et en une seule étape.

>> De gauche à droite : le chef de projet Carsten Wendt, le président de l’entreprise Dipl.-Ing. Jürgen Röders, et le chef de vente Dr. Oliver Gossel (Photo : Klaus Vollrath)
« Les aspects déterminants à prendre en compte pour la fabrication des roues dentées destinées à un usage industriel, par exemple pour la construction mécanique, sont généralement la rapidité et la flexibilité », explique Jürgen Röders, qui dirige la société Röders GmbH implantée à Soltau en Allemagne. Alors que dans des secteurs tels que l’industrie automobile, il est important de pouvoir produire de gros volumes, les séries sont beaucoup plus petites en construction mécanique. Parfois, on a seulement besoin de moins de dix exemplaires, voire d’une pièce unitaire.
Les délais exigés sont souvent courts ici et un usinage en plusieurs étapes s’avère un handicap, de même que la fabrication préalable d’outils élaborés, dotés d’une géométrie spécifiquement adaptée. Selon Jürgen Röders, il est intéressant, notamment pour les ateliers à la demande qui se sont spécialisés dans la fabrication de roues dentées en petites séries dans des délais courts, de disposer d’un équipement qui permette de fabriquer, en un jour ouvrable environ, une roue dentée de taille moyenne et de bonne qualité, à partir d’une pièce brute déjà trempée.
L’usinage de roues dentées avec le logiciel de FAO Euklid Gear…
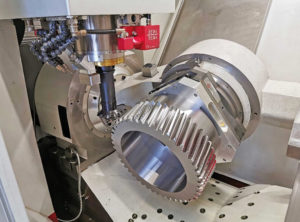
>> Les centres de fraisage 5 axes de Röders permettent de produire dans un délai court des roues dentées de grande qualité à partir de pièces brutes en acier trempé (Photo : Klaus Vollrath)
« Pour fabriquer des roues dentées, il faut un logiciel de FAO conçu spécialement pour cela, qui couvre également les différentes variantes de correction des flancs de dents », précise Carsten Wendt, qui est en charge de ce projet de développement. Le partenaire technologique de l’entreprise pour ce projet est le développeur de logiciels de FAO Euklid, qui a mis au point Euklid Gear-CAM, un programme élaboré spécialement pour répondre à ces exigences. Ce module de logiciel convivial assiste l’utilisateur lors de la fabrication de roues dentées de haute précision sur des fraiseuses standard.
Cette solution est particulièrement intéressante pour les entreprises qui ont besoin rapidement – en parallèle ou en complément de leur production habituelle – d’une pièce unitaire ou de petites séries, qu’il s’agisse de prototypes, de modèles spéciaux ou de pièces de rechange pour réparer des engrenages existants. Le programme prend également en compte les fonctions correctives essentielles du profil de la denture telles qu’une géométrie bombée en hauteur ou en largeur, ainsi que la dépouille de tête et de pied. L’un des autres avantages d’un centre d’usinage 5 axes est qu’il évite de devoir corriger l’intrication du flanc des dents.
…nécessite en premier lieu un centre d’usinage 5 axes de haute précision

>> Ce pignon droit en 16MnCr5, doté d’une denture à chevrons (Ø450 mm), a été fraisé en 18 heures et 45 minutes sur une Röders RXU 1001 DSH (Photo : Klaus Vollrath)
« La précision du centre d’usinage joue un rôle déterminant dans la fabrication de roues dentées », indique le directeur commercial Dr.-Ing. Oliver Gossel. Et d’ajouter que « comme les installations de Röders sont développées pour des secteurs tels que la fabrication de moules et d’outils dont le niveau d’exigence est particulièrement élevé, elles satisfont d’entrée de jeu aux spécifications les plus strictes en matière de précision, de dynamique, et affichent une grande endurance ». Sur ce segment de marché, la dureté des matériaux à usiner peut dépasser 60 HRC, alors que la précision à respecter peut descendre jusqu’au micron. Par ailleurs, les machines employées pour ce projet, comme par exemple le RXP 601 DSH, conviennent non seulement au fraisage mais aussi à la rectification par coordonnées. Leur précision est garantie par un ensemble de caractéristiques de conception, qu’il s’agisse de leur bâti massif en béton polymère, de leur système de guidage de haute précision, de leur dispositif d’entraînement linéaire direct sans frottement ou encore d’une gestion thermique sophistiquée au moyen de canaux de refroidissement internes dans tous les composants critiques. Des éléments intermédiaires tempérés empêchent la diffusion de chaleur en provenance des entraînements dans le bâti de la machine. Une attention particulière est également portée à l’allongement de la broche principale qui varie en fonction de la température et qui est surveillé par un capteur et compensé par la commande.
Il est à noter aussi que la cadence élevée des intervalles de réglage (« Racecut »), dont la fréquence s’élève à 32 kHz, permet de détecter et de corriger rapidement la moindre déviation de trajectoire. Les règles de mesure graduées en verre, d’une résolution de 5 nanomètres et le système breveté d’équilibrage de l’axe Z viennent compléter ces atouts. La compensation globale de tous les écarts de positionnement et d’angle du plateau rotatif pivotant joue également un rôle important. Pour cela, l’unité est testée lors de sa fabrication avec plus de 400 positions différentes des deux axes rotatifs, et des mesures sont effectuées à chaque fois avec la plus grande précision.
Précision lors du changement d’outil
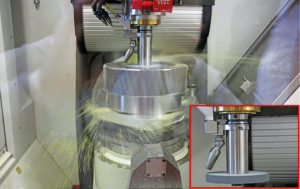
>> La roue de meulage pour la rectification cylindrique intérieure ou extérieure dispose de sa propre alimentation d’huile intégrée qui est changée avec l’outil (Photo : Klaus Vollrath)
« Étant donné que l’usinage de dentures nécessite des outils d’un diamètre beaucoup plus grand que pour une opération de fraisage courante, un magasin supplémentaire est prévu pour ces outils-là », confie J. Röders. Ce magasin situé sous le portique peut contenir trois outils dont le diamètre peut aller jusqu’à 200 mm. Cela permet de laisser les outils courants de plus petit diamètre dans le magasin intérieur à chaîne de la machine comme d’habitude. La position du magasin et son volet de protection empêchent la pénétration de petites impuretés ou de copeaux qui pourraient engendrer des défauts d’angle entre l’interface et l’outil. Autre avantage : grâce au réglage vectoriel de la broche principale, le transfert de ces outils spéciaux s’effectue toujours selon le même angle rotatif. Cela évite les écarts d’alignement sur les outils de rectification, même après plusieurs changements d’outil.
EQUIP PROD • N°130 Septembre 2021