Haas aide Gaes à réaliser des appareils auditifs sur mesure
HAAS AUTOMATION / GAES
par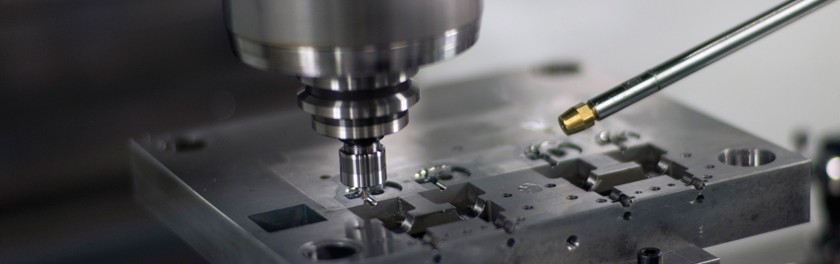
La technologie Haas a permis à Gaes d’accélérer le processus d’usinage de pièces complexes et de haute précision
Autrefois, cornets acoustiques en cuivre, aujourd’hui, implants cochléaires : aucun doute, les appareils auditifs ont parcouru un très long chemin. Le fabricant espagnol Gaes innove depuis soixante ans. Depuis sa fondation, la société n’a eu de cesse d’appliquer toutes les technologies disponibles afin de rendre les appareils auditifs plus petits, moins gênants et plus efficaces. Son dernier investissement a porté sur un centre d’usinage CNC Haas VF-2SS.
Appartenant à Gaes, l’usine Microson est implantée sur cinq étages, dans la région de Barcelone. Le nouveau siège social a ouvert en 2010 et rend hommage à son fondateur, Juan Gassó. Une vitrine installée à l’accueil expose ainsi sa moto restaurée, célébrant l’homme, sa vision et les efforts qu’il a consentis. Une longue galerie vitrée courant le long d’un mur adjacent montre par ailleurs l’évolution du produit Gaes au fil des décennies. Cinquante ans après les débuts d’importateur de Juan Gassó, le marché mondial des appareils auditifs pèse 5,4 milliards $ par an, Gaes représentant la société leader en Espagne. Au sein des salles propres et des laboratoires électroniques de son usine, 130 employés produisent plus de 50 000 appareils auditifs chaque année.
Le nouveau bâtiment abrite la machine Haas de la société : un centre d’usinage vertical à grande vitesse VF2-SS. Microson cible une production journalière de cinquante à soixante unités pour ses produits standard. La fraiseuse Haas est en revanche utilisée pour réaliser des produits personnalisés, à savoir des dispositifs sur mesure ajustés aux dimensions auriculaires exactes des utilisateurs. « Le processus démarre dès lors que l’un de nos centres auditifs nous envoie l’empreinte auriculaire d’un patient, explique Sergio Pavon, assistant technique au département R&D. Il s’agit d’un négatif 3D du canal auditif, créé à partir d’un genre de résine. Dans notre système de CFAO, nous numérisons ensuite le négatif afin d’obtenir un fichier 3D, qui nous sert à programmer la machine Haas. Grâce à la machine Haas, il s’écoule dorénavant trois à quatre jours seulement entre la commande et la livraison des dispositifs personnalisés. Avec elle, nous pouvons contrôler l’intégralité du procédé de fabrication. »
Outre la réduction du délai de fabrication des pièces, la machine Haas contribue également à assurer une meilleure uniformité du produit. « Avant l’avènement de la technologie de fabrication assistée par ordinateur, il était facile d’identifier qui avait réalisé tel dispositif, poursuit Sergio Pavon. Aujourd’hui, avec l’impression 3D, l’aspect final des instruments auditifs est standardisé, ce qui permet une meilleure qualité et une réduction des rebuts ».
Répondre aux besoins de l’entreprise
La machine Haas a été installée en 2013. Au départ, le but était d’acquérir une machine de bonne qualité à la fois précise et conviviale. Simple et intuitive, celle-ci avait permis une mise en œuvre très rapide et de ne pas consacrer trop de temps de formation pour rendre un opérateur compétent. La vitesse, le niveau d’exactitude et la précision répondent à tous les besoins de l’entreprise. La machine est en outre polyvalente, ce qui permet de changer d’application facilement.
Bien que le centre VF2-SS est utilisé pour de nombreuses tâches d’usinage quotidiennes, comme la coupe d’acier, d’aluminium et de plastique, il sert majoritairement à l’usinage de moules. Ces derniers interviennent ensuite dans la production de petites pièces très délicates qui composent les appareils auditifs de la société, par le biais de machines de moulage par injection classiques et de machines par ultrasons spéciales à froid.
La méthode par ultrasons a été introduite initialement pour réaliser une minuscule pièce circulaire en plastique, dotée d’une membrane en treillis qui s’étire le long de la partie microphone du dispositif auditif pour protéger ce dernier du vent, de l’eau et de la poussière. « Ce composant exige le recours à un plastique très onéreux, confie Sergio Pavon. Il doit être non allergène et conforme à certaines directives sanitaires de l’industrie. Le moulage classique ne convient pas ici, du fait du taux trop important de rebuts causés par la chaleur inhérente du procédé, qui endommage la pièce. »
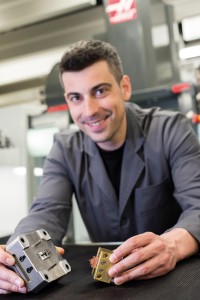
Ivan Jimenez, responsable d’atelier avec quelques pièces dont une électrode, usinées sur machine Haas
Un choix difficile
Avec la machine par ultrasons conçue spécialement pour la société, aucune chaleur n’est générée. La résine est en effet liquéfiée par une électrode vibrant 30 000 fois par seconde. L’entreprise utilise cette machine pour développer et fabriquer le filtre et le raccord du conduit auditif interne. Les électrodes produites pour la machine à ultrasons sont également usinées à l’aide du centre VF2-SS, qui fonctionne en grande partie sans surveillance, à raison de deux rotations chaque jour.
Ivan Jimenez, responsable de l’atelier d’usinage, explique comment la société s’y est pris pour faire son choix parmi les différents modèles et marques de machines. « Quand nous cherchons une nouvelle machine, notre première tâche consiste à remplir un rapport de vérification dans lequel le fournisseur, dans ce cas, Haas, doit compléter une série d’exigences auxquelles nous voulons que la machine se conforme, développe-t-il. Sur la base de cette évaluation, nous rédigeons ensuite une feuille de calcul dans laquelle nous commençons à attribuer des points à chaque machine. Nous poursuivons ce processus jusqu’à ce que nous soyons assurés que la décision définitive d’achat repose sur des facteurs purement objectifs, tels que le régime, la puissance, la précision et la répétabilité, et non sur des facteurs subjectifs comme l’aspect visuel. »
Le choix fut relativement difficile, concède Lluis Gómez, directeur du produit Microson. « Au final, c’est le rapport qualité-prix qui nous a décidés, ainsi que le délai de livraison, qui constituait également un critère très important. Mais nous sommes très satisfaits d’avoir opté pour la technologie Haas, qui nous a permis d’accélérer l’usinage de nos pièces délicates et de haute précision. »
En 2008, le fondateur de Gaes, Juan Gassó, est décédé. Au moment de sa mort, la société comptait plus de 500 centres auditifs de par le monde. Gaes possède aujourd’hui des bureaux au Portugal, en Turquie, au Chili et en Argentine, desservant plus de 500 000 clients. La réussite de l’entreprise tient pour beaucoup aux efforts infatigables de son fondateur, ainsi qu’à sa foi en la technologie. Gaes propose aujourd’hui des appareils auditifs numériques discrets, qui permettent à un nombre considérable de personnes de mener une vie plus sûre, plus heureuse et de bien meilleure qualité. |
N° 64 mars 2015