Un outil exceptionnel dédié à l’assemblage des modules-rotors, à découvrir au Bourget
MARPOSS
parParmi les pièces les plus sensibles du Rotor, le compresseur haute pression est la partie chaude du moteur, particulièrement stratégique. Fiabilité et endurance doivent pouvoir être assurées. L’assemblage est alors une étape délicate. Ainsi, quelle solution adopter pour placer et serrer, en toute sécurité, la série d’écrous nécessaires à l’assemblage du Rotor HP GE 115, au coeur de cette pièce complexe ?
À cette question, que se posait Safran Aircraft Engine, Marposs a su apporter une réponse renouvelée et performante : la clé de serrage Disque 6. Cet outil dédié, créé en très petite série (deux à trois exemplaires) a été lancé pour la première fois en 2011. Fruit d’un partenariat avec le constructeur, il bénéficie d’optimisations régulières qui lui permettent notamment de s’adapter à l’évolution du moteur. Dernière amélioration en date, en 2016, l’ajout de mini-caméras HD, un confort décisif pour les utilisateurs.
Le rôle précis de l’outil Marposs ? L’assemblage du spool-étage 2-5 (partie supérieure du rotor) avec le disque 6 et le spool 7-9 (cf visuel), le tout constituant le rotor compresseur HP. La tâche est délicate : la clé doit venir serrer 66 écrous. À l’aveugle de surcroît, car le travail s’effectue par le dessus du module assemblé.
Une répétabilité maximisée de l’opération
L’outillage proposé par Marposs offre un couple de serrage à 42 Nm avec une grande précision du rendement résiduel. Il serre à un couple défini et contrôlé, répétable avec une tolérance de 5% maximum. Les matériaux choisis pour la conception accroissent encore la possibilité d’obtenir une répétabilité maximale. Plus d’une centaine d’éléments différents composent la clé de serrage Disque 6. Des matériaux rigides et légers sont utilisés tel que l’aluminium aéronautique. La tête, en acier traité nitruré, est revêtue de balinit C, ce qui renforce sa dureté. On atteint ainsi un rendement parfait du train de pignons de la tête de serrage et un glissement optimisé pour une répétabilité maximisée. Autre challenge : comment insérer la tête de clé dans le rotor, passer dans un diamètre étroit, tout en allant serrer les écrous aux extrémités du spool ? La solution : la clé est munie d’une tête de serrage à cassettes escamotables.
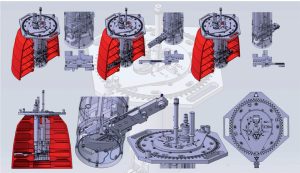
À l’intérieur du module-rotor corps HP : process de mise en place et de serrage des 66 écrous – © Marposs
Trois mini-caméras HD pour gagner en temps, fiabilité, sécurité et confort !
Reste une problématique, et non des moindres : fixer les écrous sans visibilité. Si Marposs proposait dans un premier temps d’associer son outil à un endoscope, ses équipes R&D réfléchissaient depuis 2013 à l’utilisation de caméras. Depuis 2016, cette option a été affinée : trois mini-caméras HD couleur, de diamètre 5 équipent désormais la clé. Elles permettent de contrôler les cycles de serrage et le bon chargement de l’écrou mais aussi de vérifier qu’il n’y a pas d’impureté à l’intérieur du module. Le risque de faire tomber un écrou dans le moteur est ainsi écarté.
Avantage supplémentaire : l’assemblage complet du disque 6 et spool 7/9 ainsi que la mise en place et le serrage des 66 écrous peuvent être réalisés en une seule fois, sans sortir la clé du module, pour un gain de temps moyen estimé à 30%. Cerise sur le gâteau : les caméras autorisent l’enregistrement et apportent donc une traçabilité du cycle. La fiabilité et la sécurité de l’opération de serrage sont renforcées et le confort au travail des opérateurs est amélioré.
Des outillages d’exception, entièrement conçus chez Marposs à Chelles, un savoir-faire unique
Conçue à 100% chez Marposs à Chelles (Seine-et-Marne), cette typologie d’outillages aéronautiques bénéficie d’un savoir-faire unique en France et très rare dans le monde. De l’ingénierie à la validation du client en passant par la fabrication, l’assemblage et les tests, tout est réalisé dans les locaux de l’entreprise, en région parisienne. Quatre versions différentes de ces outils très complexes, produits phares, nés d’un développement Marposs existent aujourd’hui, pour les moteurs GE115, GE 94, GP 7002 et M88 (moteur militaire). D’autres moteurs pourraient demain profiter des avantages majeurs de cette technologie d’exception !
N° 89 Mai 2017